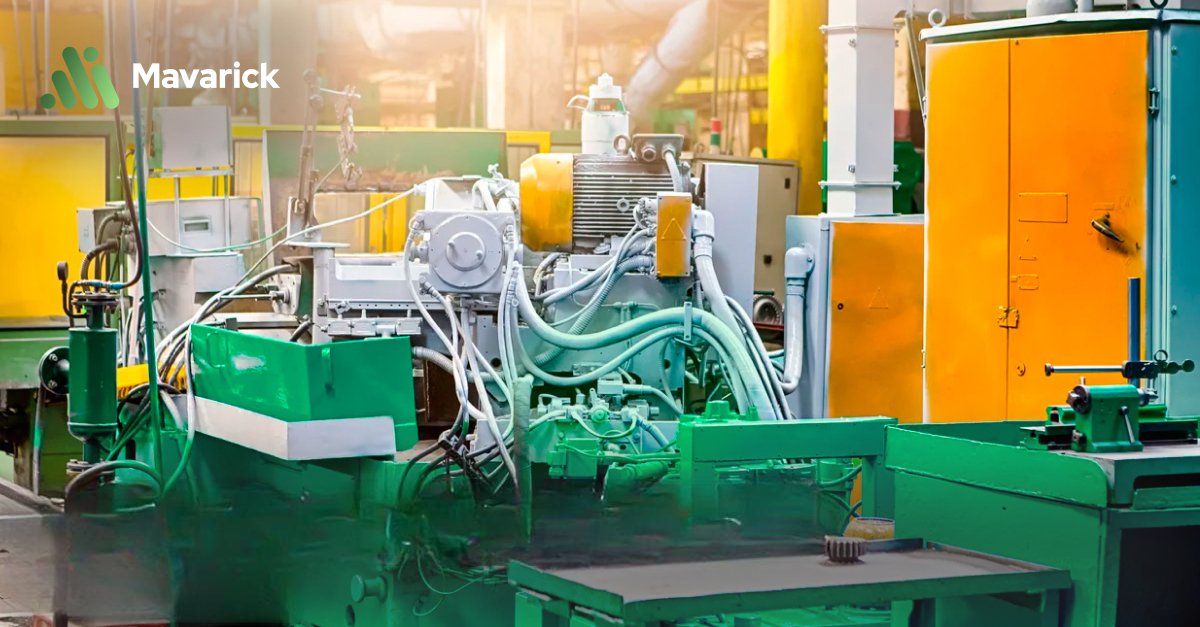
Table of Contents
- What is an Energy Management System (EMS)?
- Key Components of an EMS:
- Role of EMS in Manufacturing
- Benefits of Implementing an EMS
- Challenges in Scaling EMS in Large Organizations
- Effective Solutions
- Real-World Examples of EMS Benefits
- Key Components of an Energy Management System (EMS)
- 1. Energy Monitoring and Metering
- 2. Energy Audits
- 3. Energy Efficiency Measures
- 4. Integration with Carbon Reporting
- 5. Automation and Smart Technology
- Applications of Energy Management Systems- Industry-Specific
- Trends in Energy Management System
- Steps to Implement an Effective Energy Management System (EMS)
- Step 1: Conduct an Energy Audit to Assess Current Usage
- Step 2: Set Energy Reduction and Carbon Reporting Goals
- Step 3: Select the Right EMS Tools and Technology
- Step 4: Train Employees and Create an Energy-Conscious Culture
- Step 5: Monitor, Review, and Optimise the EMS Regularly
- ROI of Energy Management Systems
- How to Use EMS for Lowering Manufacturing Costs?
- Future of Energy Management Systems
- Emerging Technologies in EMS
- Anticipated Regulatory Shifts
- Role of EMS in Net Zero and Carbon Neutrality
- Conclusion
As businesses grapple with rising energy costs and stricter emissions standards, adopting EMS has become essential. These systems help organisations monitor and optimise their energy consumption and significantly reduce their carbon footprint, enabling compliance with carbon emissions reporting frameworks and fostering the transition to renewable energy sources.

Did you know?
The potential of EMS is reflected in its rapid market growth. The global Energy Management System market was valued at USD 31.76 billion in 2023 and is projected to grow to an impressive USD 112.32 billion by 2032, with a compound annual growth rate (CAGR) of 15.3%.
This trajectory highlights the increasing reliance on EMS to not only enhance efficiency but also tackle critical issues like carbon emissions, regulatory compliance, and the adoption of renewable energy sources.
For manufacturers, in particular, the integration of energy management systems in manufacturing is transformative. By streamlining processes, reducing CO2 emissions from fossil fuel combustion, and supporting greenhouse gas reduction goals, EMS are paving the way for sustainable industrial practices.
Whether you’re looking to lower costs, meet regulatory requirements, or align with global sustainability goals, EMS offer a powerful, data-driven solution.
Let's delve in!
What is an Energy Management System (EMS)?
An Energy Management System (EMS) is a strategic framework or software solution designed to monitor, control, and optimise energy consumption in real time. EMS provides organisations with actionable insights to improve energy efficiency, reduce costs, and achieve sustainability goals. EMS empowers businesses to proactively manage their energy usage from large-scale manufacturing facilities to office buildings while minimising their environmental impact.
There are different ways to analyse and understand energy usage in manufacturing. Below is a list of common ways that manufacturers analyse energy usage. These terms and their definitions may seem rudimentary, but using precise terms can help ensure your team communicates effectively.

Key Components of an EMS:
- Data Monitoring and Collection: Sensors and IoT devices track energy consumption across operations.
- Analysis Tools: Advanced software identifies patterns, inefficiencies, and potential savings opportunities.
- Control Mechanisms: Automated systems regulate energy-intensive processes like lighting, HVAC, and machinery.
- Reporting Features: Generate reports to meet regulatory requirements like the GHG Protocol and track progress towards energy goals.
Role of EMS in Manufacturing
EMS plays a critical role in tracking and analysing energy consumption, enabling businesses to pinpoint inefficiencies and implement corrective measures. For instance, an EMS can reduce energy waste in manufacturing by automating shutdowns during idle times or optimising production schedules. These insights lead to tangible benefits, such as lower operational costs and improved compliance with energy efficiency standards.
So, now the question is how does EMS help in carbon reduction?
- By reducing energy waste and promoting the use of renewable energy sources, EMS directly contributes to lowering an organisation’s carbon footprint. This is especially crucial in manufacturing, where energy-intensive processes often result in significant CO2 emissions from fossil fuel combustion.
- EMS aligns seamlessly with reporting standards like the GHG Protocol, ensuring accurate measurement and reporting of greenhouse gases. It aids compliance by tracking emissions data and reducing operational energy usage, promoting long-term sustainability.
Implementing an EMS not only optimises energy performance but also positions businesses as leaders in energy efficiency and sustainability.
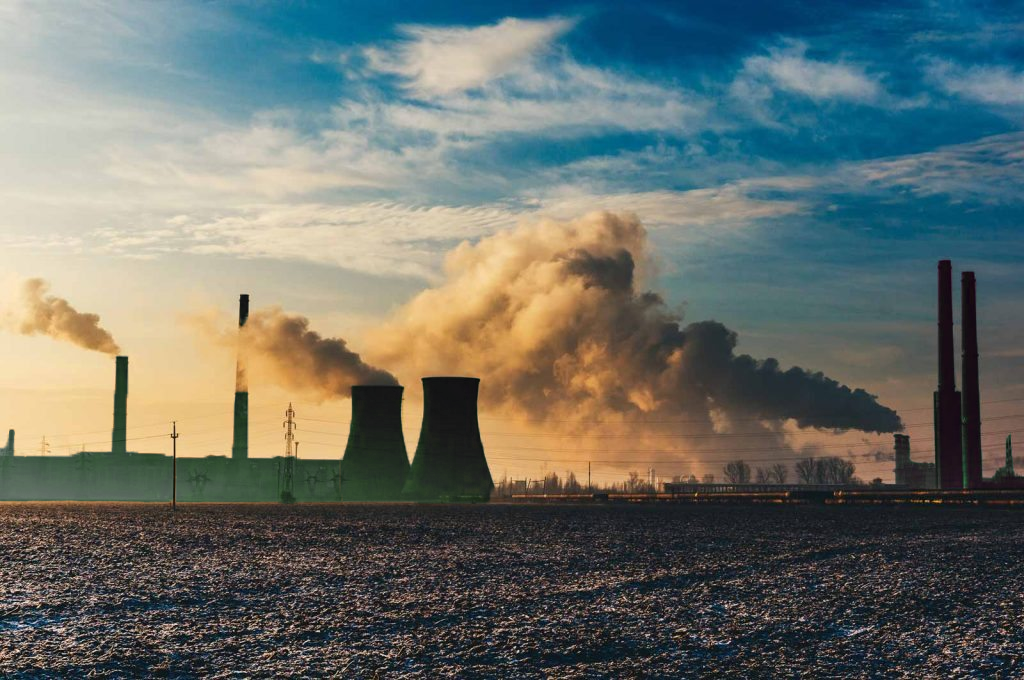
Benefits of Implementing an EMS
Implementing an Energy Management System (EMS) offers numerous advantages that enhance operational efficiency and sustainability. Key benefits include:
- Energy Savings and Cost Reductions: EMS enables organisations to monitor and optimise energy consumption, effectively reducing waste. This leads to significant cost savings by lowering utility expenses and improving overall energy efficiency.
- Environmental Impact Mitigation: By decreasing energy usage, EMS contributes to lowering greenhouse gas emissions and reducing the carbon footprint. This aligns with global efforts to combat climate change and promotes corporate environmental responsibility.
- Regulatory Compliance: EMS assists businesses in adhering to standards such as the Streamlined Energy and Carbon Reporting (SECR), Corporate Sustainability Reporting Directive (CSRD), and ISO 50001. Compliance with these regulations ensures legal adherence and enhances corporate reputation.
- Operational Efficiency: In manufacturing facilities, EMS improves energy usage by identifying inefficiencies and implementing optimisation strategies. This leads to enhanced productivity and reduced operational costs.
- Strategic Decision-Making: EMS provides real-time data analytics, empowering organisations to make informed decisions regarding energy management. This supports long-term sustainability planning and resource allocation.
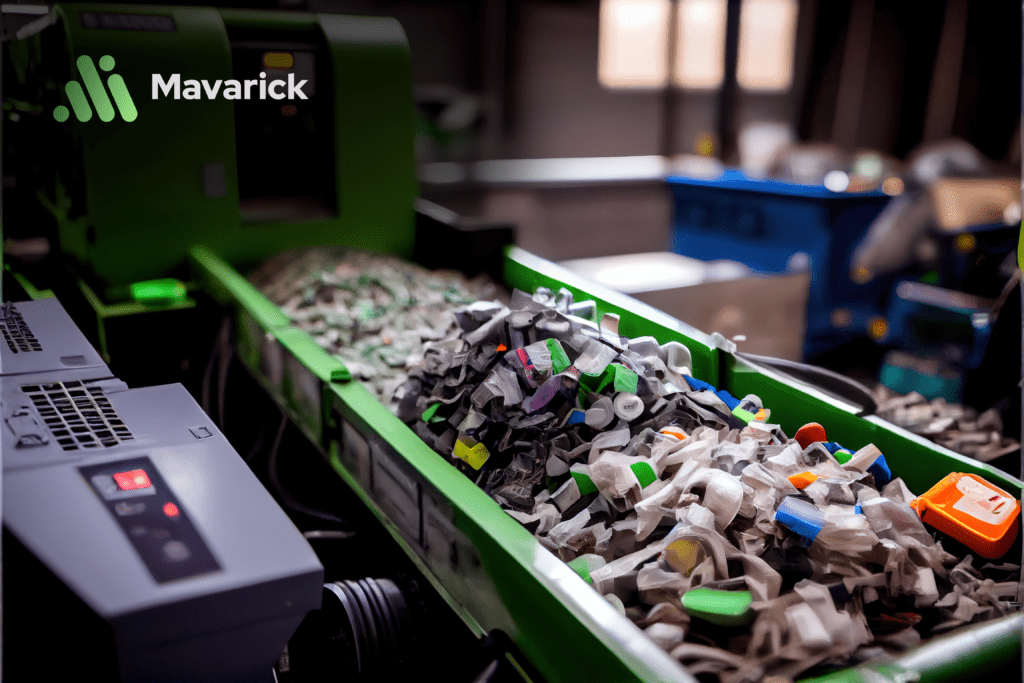
Challenges in Scaling EMS in Large Organizations
While Energy Management Systems (EMS) offer immense benefits, their implementation can pose several challenges. Recognising these obstacles and addressing them strategically ensures a smoother transition to energy-efficient operations.
- High Initial Investment: The cost of installing sensors, meters, and advanced software can be prohibitive for some organisations. However, these upfront expenses often yield long-term savings and sustainability gains.
- Integration with Existing Systems: Many businesses struggle to align EMS with their current infrastructure, leading to inefficiencies during the initial phases.
- Data Accuracy Issues: Inconsistent or incomplete energy data can hinder the effectiveness of EMS, especially when integrating it with Scope 1, 2, and 3 emissions reporting frameworks like the GHG Protocol.
Effective Solutions
- Government Incentives:
Leverage subsidies and tax breaks designed to promote energy efficiency. For instance, the EU offers funding schemes like the Horizon Europe program to support sustainable projects, which can offset EMS implementation costs.
- Robust Planning:
A phased approach to EMS implementation, starting with an energy audit, ensures a better understanding of existing systems and paves the way for seamless integration.
- Aligning EMS with Sustainability Goals:
Positioning EMS as a tool to achieve regulatory compliance, reduce carbon emissions, and lower operational costs can drive its adoption.
Mavarick streamlines EMS implementation with seamless integration, accurate emissions data, and tailored insights, helping organisations achieve energy efficiency and sustainability goals with ease.
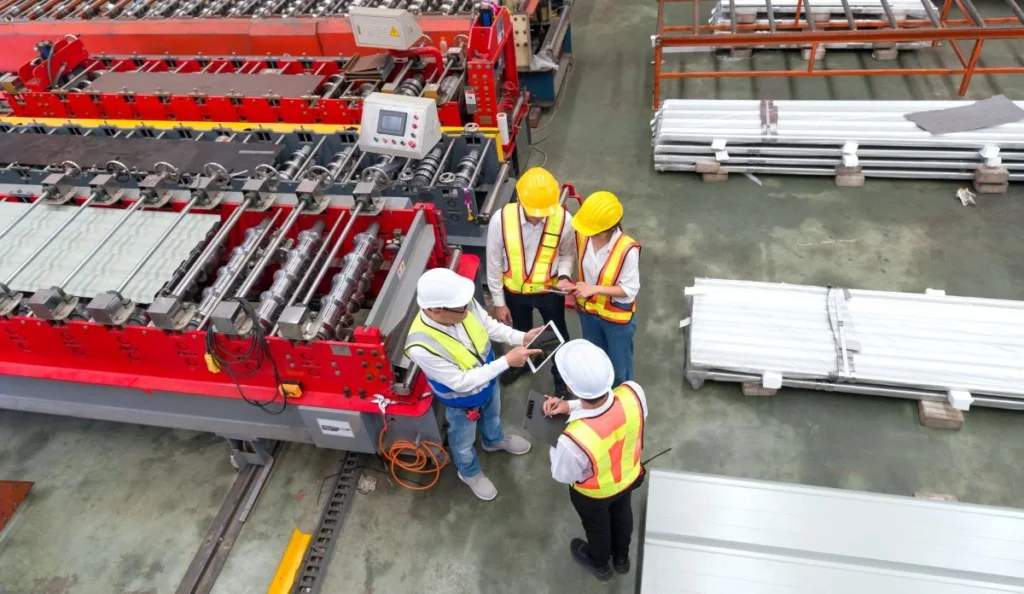
Real-World Examples of EMS Benefits
- 3M Company: By implementing an EMS across 56 sites globally, 3M achieved substantial energy savings and enhanced energy efficiency. The system facilitated continuous improvement in energy performance, contributing to the company's sustainability goals.
- Beijing Capital International Airport Co., Ltd.: The adoption of an EMS led to significant energy-saving benefits, including a reduction in energy consumption and improved energy management practices. This initiative supported the company's commitment to environmental sustainability.
- HARBEC Inc.: Through the implementation of an EMS, HARBEC achieved energy savings and improved operational efficiency. The system enabled real-time energy consumption monitoring, leading to informed decision-making and cost reductions.
These case studies demonstrate the tangible benefits of EMS implementation, including cost savings, enhanced energy efficiency, and support for sustainability objectives.
Key Components of an Energy Management System (EMS)
A well-implemented Energy Management System (EMS) is a combination of tools, processes, and strategies that work together to optimise energy consumption and improve sustainability. By leveraging the following components, organisations can achieve operational excellence and reduce their environmental impact.
1. Energy Monitoring and Metering
Accurate data collection is the foundation of any EMS. Smart meters and sensors continuously track energy consumption across operations, providing real-time data for analysis. This granular visibility helps businesses identify usage patterns, detect wastage, and set benchmarks for improvement. Effective monitoring also supports compliance with energy efficiency standards and improves decision-making.
2. Energy Audits
Regular energy audits are essential for identifying inefficiencies and uncovering opportunities to reduce energy waste. Audits assess energy usage, equipment performance, and process efficiency, enabling businesses to implement corrective actions. Mavarick's energy audit solutions streamline this process by combining comprehensive assessments with actionable insights.
3. Energy Efficiency Measures
Implementing measures like upgrading to energy-efficient equipment, optimising production schedules, and improving HVAC systems can significantly reduce energy usage. These measures are key to lowering operating costs and enhancing overall sustainability. Organisations with EMS can track the effectiveness of these measures in real-time, ensuring continuous improvement.
4. Integration with Carbon Reporting
A robust EMS aligns energy data with Scope 1, 2, and 3 emissions for comprehensive carbon reporting. This integration simplifies compliance with frameworks like the GHG Protocol, enabling businesses to track their carbon footprint and meet emissions standards. Mavarick offers seamless integration of energy management with carbon accounting software, making Scope 3 emissions reporting accurate and hassle-free. Explore our carbon reporting solutions.
5. Automation and Smart Technology
IoT devices, AI-driven analytics, and real-time automation are revolutionising EMS. Smart technologies enable predictive maintenance, automated controls, and instantaneous adjustments, maximising energy efficiency while reducing operational downtime. Mavarick leverages advanced AI and IoT to deliver real-time analytics and automation, helping businesses optimise energy usage and align with sustainability goals. Find out how our solutions integrate smart technology in our Energy Efficiency Guide.
With the right combination of these components, an EMS not only improves operational efficiency but also positions businesses as leaders in energy efficiency and sustainability.
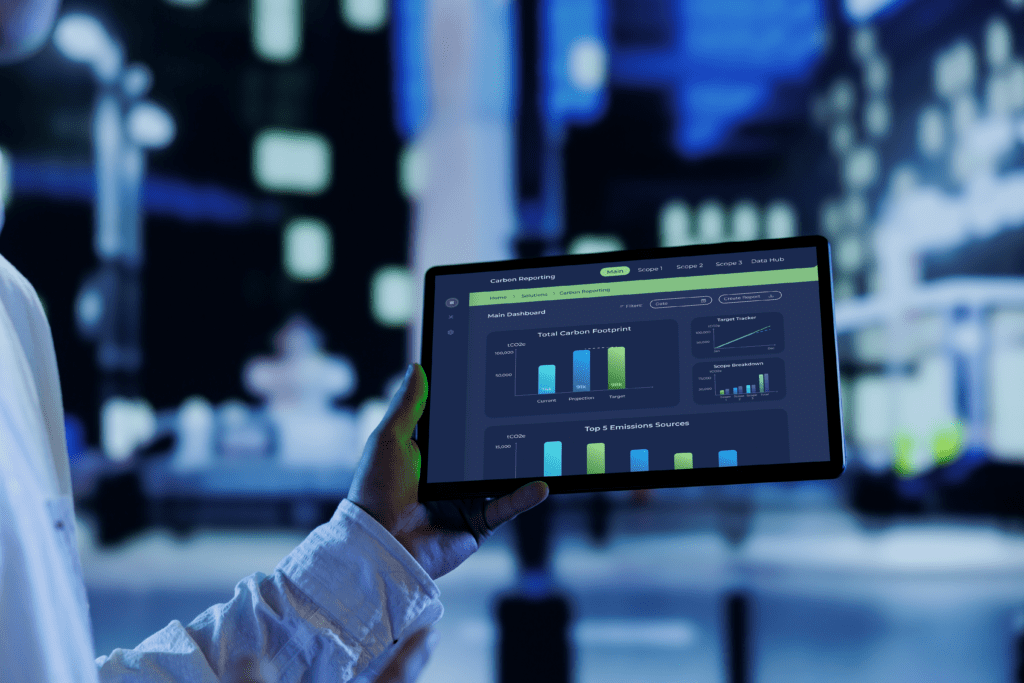
Applications of Energy Management Systems- Industry-Specific
Implementing Energy Management Systems (EMS) is essential for energy-intensive industries aiming to enhance efficiency, reduce costs, and minimize environmental impact. Here's an overview of EMS applications across various sectors:
- Manufacturing: EMS enables real-time monitoring and optimization of energy consumption in production processes, leading to significant cost savings and improved operational efficiency.
- Automotive: Incorporating EMS helps automotive manufacturers reduce energy usage in both vehicle production and operational phases, contributing to lower emissions and compliance with environmental standards.
- Aeronautics: EMS assists in managing the substantial energy demands of aircraft manufacturing, ensuring processes are energy-efficient and sustainable.
- Healthcare: Hospitals and medical facilities utilize EMS to monitor and control energy usage, ensuring critical systems operate efficiently while reducing operational costs.
- Heavy Machinery: EMS aids in optimizing the energy consumption of large equipment, enhancing performance, and extending machinery lifespan.
Did you know?
Energy Management in Automotive Manufacturing took a significant leap forward with the adoption of advanced EMS solutions by leading companies in Europe.
Volkswagen's manufacturing plant in Zwickau, Germany, has undergone a significant transformation to become a model of energy-efficient automotive production.
By implementing an advanced EMS, the plant has optimized its energy consumption, leading to a reduction in CO₂ emissions by more than 60%. This initiative aligns with Volkswagen's broader strategy to achieve carbon-neutral production across its facilities.
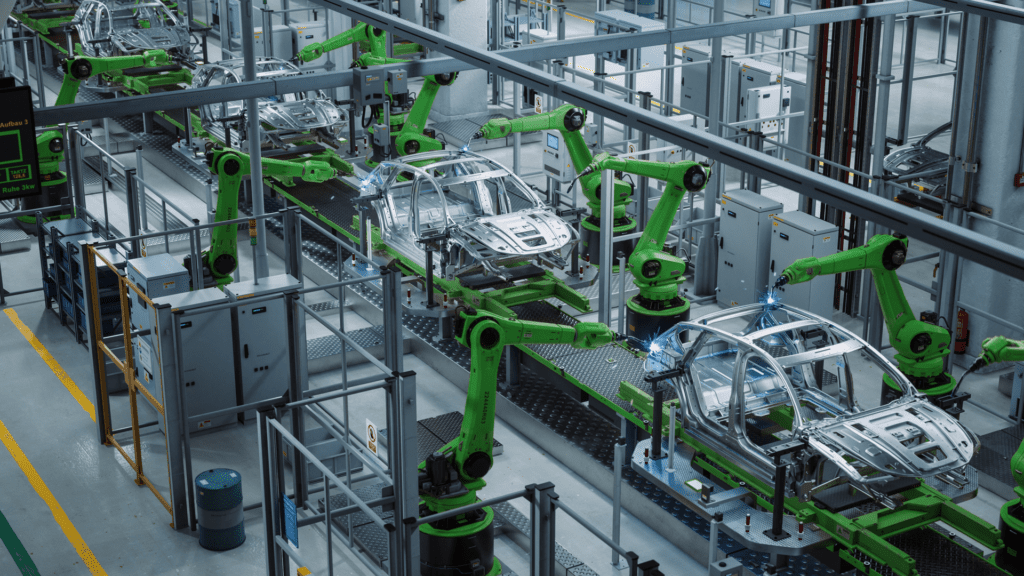
Trends in Energy Management System
The integration of renewable energy sources into Energy Management Systems (EMS) is a growing trend, driven by the global shift towards sustainable energy solutions. Key developments include:
- Increased Renewable Energy Adoption: In 2024, Spain achieved a record 56% of its electricity supply from renewable sources like wind and solar, marking a significant milestone in the country's energy transition.
- Industrial Sector Initiatives: Companies are increasingly adopting renewable energy to reduce greenhouse gas emissions. For example, Flex Power Solutions in Limerick, Ireland, developed technology to convert excess renewable electricity into useful heat, aiding industrial decarbonization efforts.
- Global Renewable Energy Capacity Growth: China has rapidly expanded its renewable energy capacity, adding 216 gigawatts of solar power in 2023 alone, demonstrating a significant commitment to renewable energy integration.
- Advancements in Energy Storage and Grid Modernization: The increasing share of renewables necessitates enhancements in energy storage solutions and grid infrastructure to manage variability and ensure reliability. Investments in smart grids and battery storage are critical to accommodate the growing influx of renewable energy.
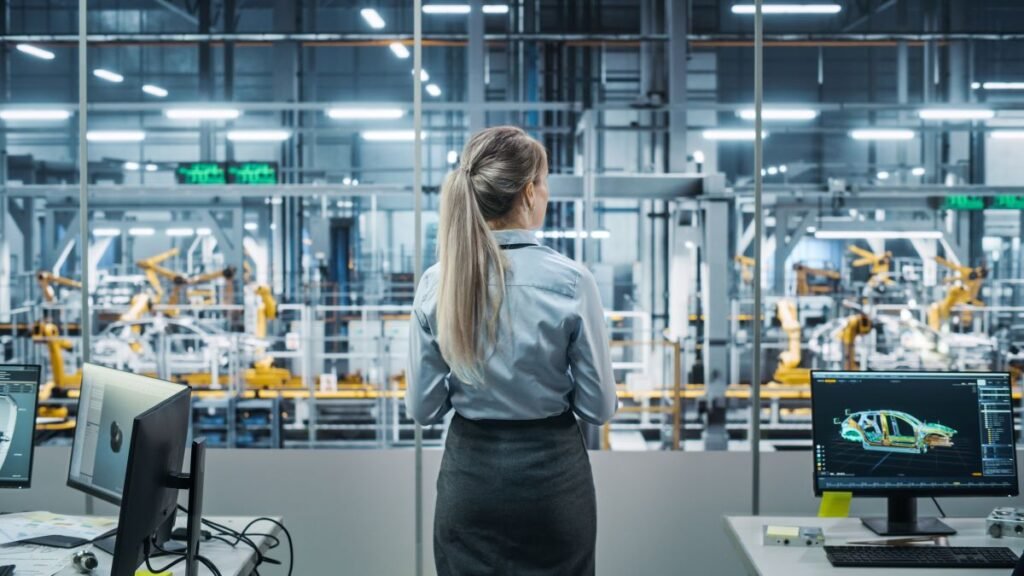
Steps to Implement an Effective Energy Management System (EMS)
Implementing an Energy Management System (EMS) requires a structured approach to ensure its effectiveness and alignment with organisational goals. Here’s a step-by-step guide:
Step 1: Conduct an Energy Audit to Assess Current Usage
Begin with a comprehensive energy audit to identify inefficiencies and establish a baseline for energy consumption. This involves examining equipment, processes, and operational practices to highlight areas of energy waste. Understanding your current energy consumption is crucial for setting actionable targets. Tools like Mavarick's energy audit solutions can provide deep insights and facilitate compliance with frameworks like the GHG Protocol.
Step 2: Set Energy Reduction and Carbon Reporting Goals
Define clear, measurable objectives for reducing energy usage and lowering carbon emissions. Goals should align with regulatory requirements such as SECR, CSRD, or ISO 50001 and consider long-term sustainability targets like net-zero emissions. Integrating these goals with Scope 1, 2, and 3 emissions reporting ensures a holistic approach to energy and carbon management.
Step 3: Select the Right EMS Tools and Technology
Choose an EMS solution that suits your organisation’s needs. Modern EMS tools leverage IoT devices, AI-powered analytics, and real-time monitoring for enhanced decision-making. Ensure the system integrates seamlessly with carbon accounting software for streamlined reporting and compliance.
Step 4: Train Employees and Create an Energy-Conscious Culture
Effective EMS implementation depends on employee engagement. Train staff to use the EMS and foster a culture of energy efficiency. Empowering employees to identify and address inefficiencies can lead to continuous improvement and stronger adherence to sustainability goals.
Step 5: Monitor, Review, and Optimise the EMS Regularly
EMS is not a one-time setup. Continuously monitor performance metrics, compare them against goals, and adjust strategies as needed. Regular reviews ensure the system evolves with changing energy demands and regulatory updates, maximising its effectiveness.
Explore Mavarick's solutions to simplify every stage of EMS implementation.
ROI of Energy Management Systems
Although many manufacturers include environmentalism in their rationale for purchasing an Energy Management System, the primary motivation for purchasing an EMS is to save on energy costs.
While the energy-saving benefits of EMS are well known, less well-known are the benefits derived from greater accuracy in job costing. Using an EMS to improve the accuracy of cost estimates can help manufacturers offer lower pricing to end customers.
This can help manufacturers that use EMS win more business. When calculating ROI for an EMS, both the cost-savings from energy use reductions and additional business won through lower pricing proposals should be considered.
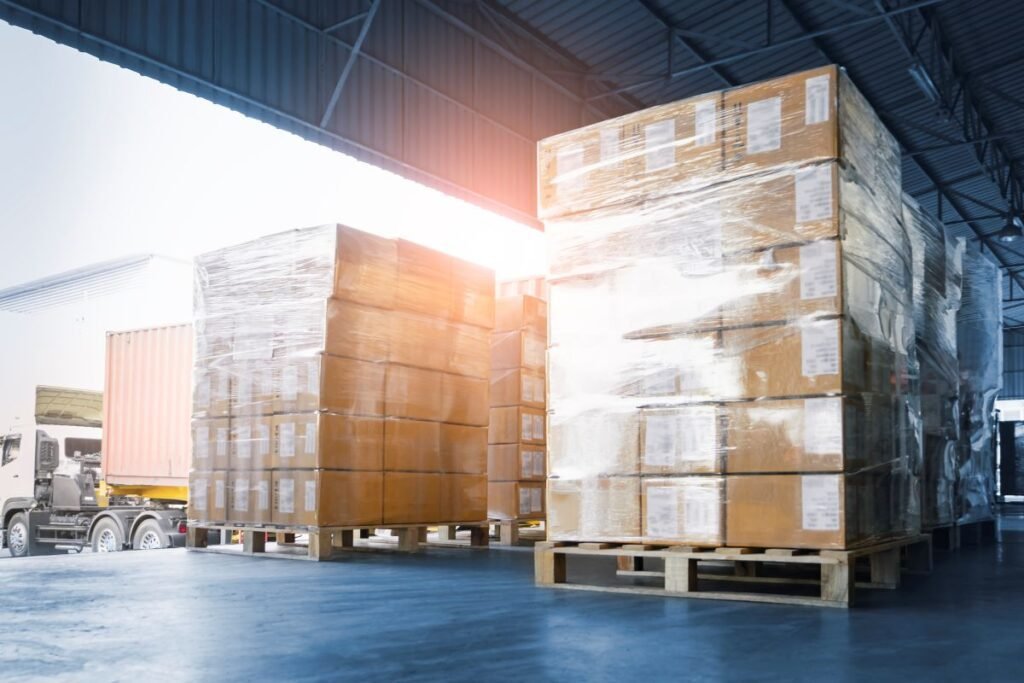
How to Use EMS for Lowering Manufacturing Costs?
Here are some of the ways that an EMS can be used to drive lower costs:
- Reduce Downtime Energy Costs: Identify periods when machines are running idle or at reduced capacity
- Shift Loads: Run the most energy-intensive processes at off-peak times
- Predictive Maintenance: Use energy draw as an indicator for when machines require maintenance
- Minimising Total Energy Overhead: Use EMS to establish benchmarks to ensure that energy usage is within parameters.
Future of Energy Management Systems
The future of Energy Management Systems (EMS) is being shaped by rapid advancements in technology and evolving sustainability goals. These innovations are set to transform how businesses manage energy and reduce their environmental impact.
Emerging Technologies in EMS
- Smart Grids: These intelligent energy networks allow EMS to interact dynamically with utilities, optimizing energy distribution and consumption while reducing waste.
- Digital Twins: Virtual replicas of physical systems enable organisations to simulate and test energy strategies, predicting outcomes without disrupting operations.
- Advanced Sensors: IoT-enabled sensors provide real-time data on energy usage, improving precision and enabling proactive energy management.
Anticipated Regulatory Shifts
Future regulations are likely to mandate stricter carbon emissions reporting and energy efficiency standards. Policies such as the European Union’s Fit for 55 package and expanded frameworks like CSRD are expected to drive EMS adoption further. Organisations that proactively implement EMS will benefit from improved compliance and competitive advantage.
Role of EMS in Net Zero and Carbon Neutrality
EMS plays a critical role in achieving net zero and carbon neutrality targets by tracking and optimising energy consumption while reducing carbon emissions. By integrating with renewable energy sources and aligning with frameworks like the GHG Protocol, EMS supports organisations in transitioning away from fossil fuels and toward sustainable energy solutions.
Conclusion
The evolving landscape of EMS underscores its importance in meeting both operational and environmental challenges. By embracing emerging technologies and aligning with regulatory goals, businesses can position themselves as leaders in energy efficiency and sustainability. Mavarick's advanced tools and solutions are at the forefront of this transition, helping organisations navigate the future of energy management with confidence. Contact Mavarick today for smarter Energy Management System solutions.
Carbon Accounting System
Carbon Emissions Reporting for the Supply Chain
- Visible Supply Chain
- Quality Data You can Trust
- Auditable Reports