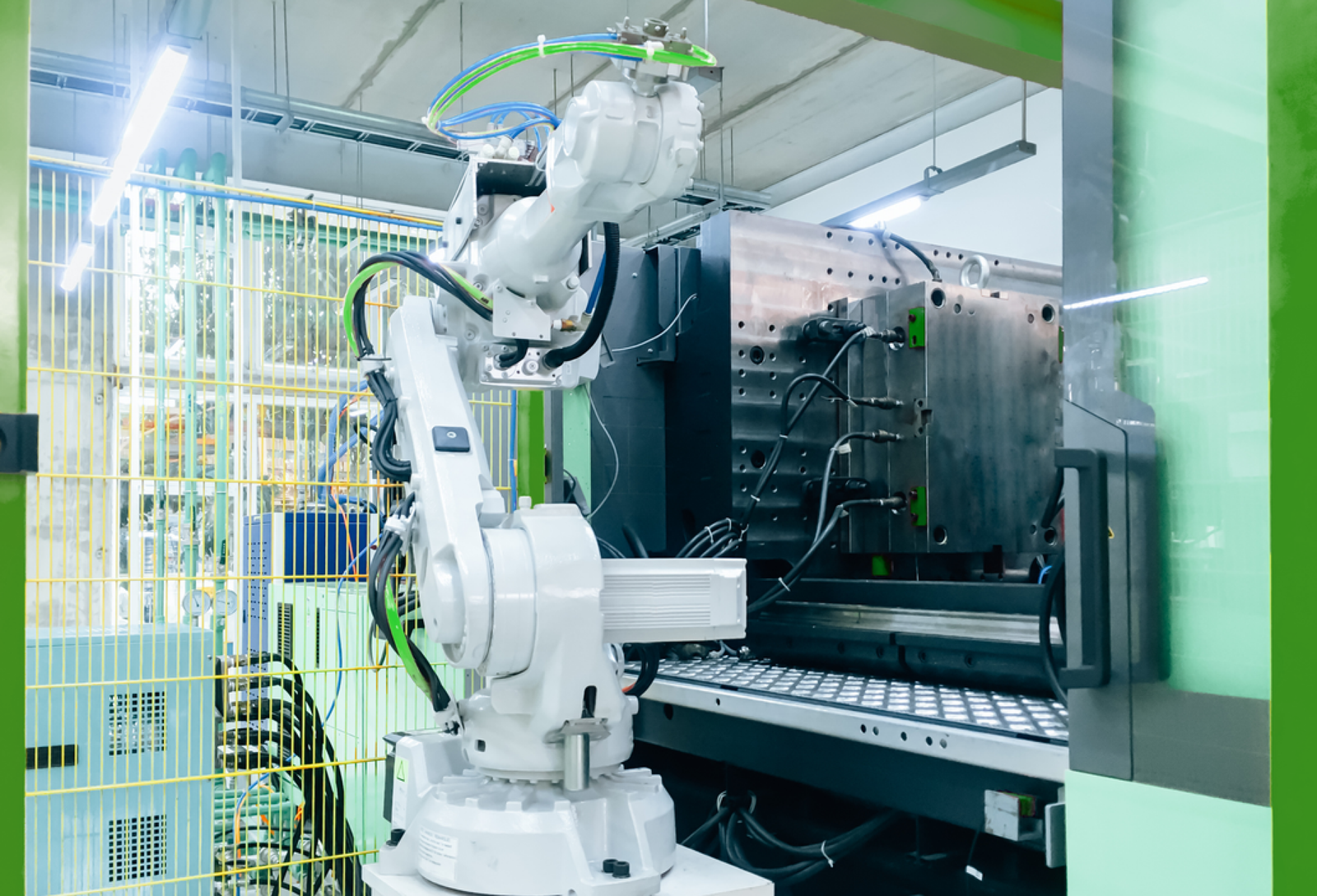
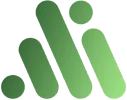
6 Ways to Reduce Scope 1 and Scope 2 Emissions in Manufacturing
Table of Contents
- Key Takeaways
- What are Scope 1, & Scope 2 Emissions?
- Why is There a Need to Reduce Scope 1 & 2 Emissions?
- Challenges While Reducing Scope 1 & Scope 2 Emissions
- 6 Ways to Reduce Scope 1 & 2 Emissions
- 1. Optimise Energy Efficiency in Operations
- 2. Switch to Renewable Energy Sources
- 3. Implement Real-Time Emissions Monitoring and Reporting Software
- 4. Upgrade to Low-Emission Equipment and Vehicles
- 5. Enhance Process Efficiency
- 6. Engage Employees in Sustainability Initiatives
- Example of Scope 1 & Scope 2 Emissions in Manufacturing
- 1. Manufacturing Industry
- 2. Automotive Industry
- 3. Aerospace Industry
- 4. Medical Industry
- 5. Plastics Manufacturing
- Laws Around Scope 1 and Scope 3 Emissions
- 1. European Union's Corporate Sustainability Reporting Directive (CSRD)
- 2. U.S. Securities and Exchange Commission (SEC) Proposed Rule
- 3. Ireland's Climate Action and Low Carbon Development (Amendment) Act 2021
- Bottom Line
- Frequently Asked Questions (FAQs)
Scope 1 and Scope 2 emissions are the bedrock of a company’s environmental impact – the emissions directly tied to the energy a business uses to function. These two categories aren't just metrics; they’re the closest reflection of a company's core carbon footprint.
Scope 1 emissions cover anything the company directly controls, like manufacturing fuel combustion or emissions from company-owned vehicles. In sectors like medical manufacturing, Scope 1 emissions are often linked to essential processes like the use of sterilizing agents, such as ethylene oxide (EtO), which ensure device safety but also release VOCs, potent greenhouse gases.
Scope 2 emissions, meanwhile, come from purchased electricity, heating, or cooling needed to run manufacturing facilities and, in the case of medical manufacturing, often power energy-intensive cleanrooms where strict climate control is essential.
Here’s where the numbers tell a striking story: energy-related CO₂ emissions from the industrial sector alone hit 9.4 billion metric tons in 2021. This is a record high that underscores why companies are racing to find ways to cut down.
With Scope 1 and 2 emissions so closely tied to everyday operations, these emissions become a powerful leverage point for businesses. For experts, addressing them isn’t just about compliance – it’s about finding smart, measurable ways to operationalise sustainability, cutting waste, and transforming efficiency into a real competitive advantage.
And this is where carbon accounting software steps in. For companies committed to reducing Scope 1 and 2 emissions, these tools provide real-time insights into energy usage, direct emissions, and the indirect impact of purchased electricity.
Let’s dive deeper into the various concepts of Scope 1 and Scope 2 emissions and how carbon accounting software is redefining emissions management.
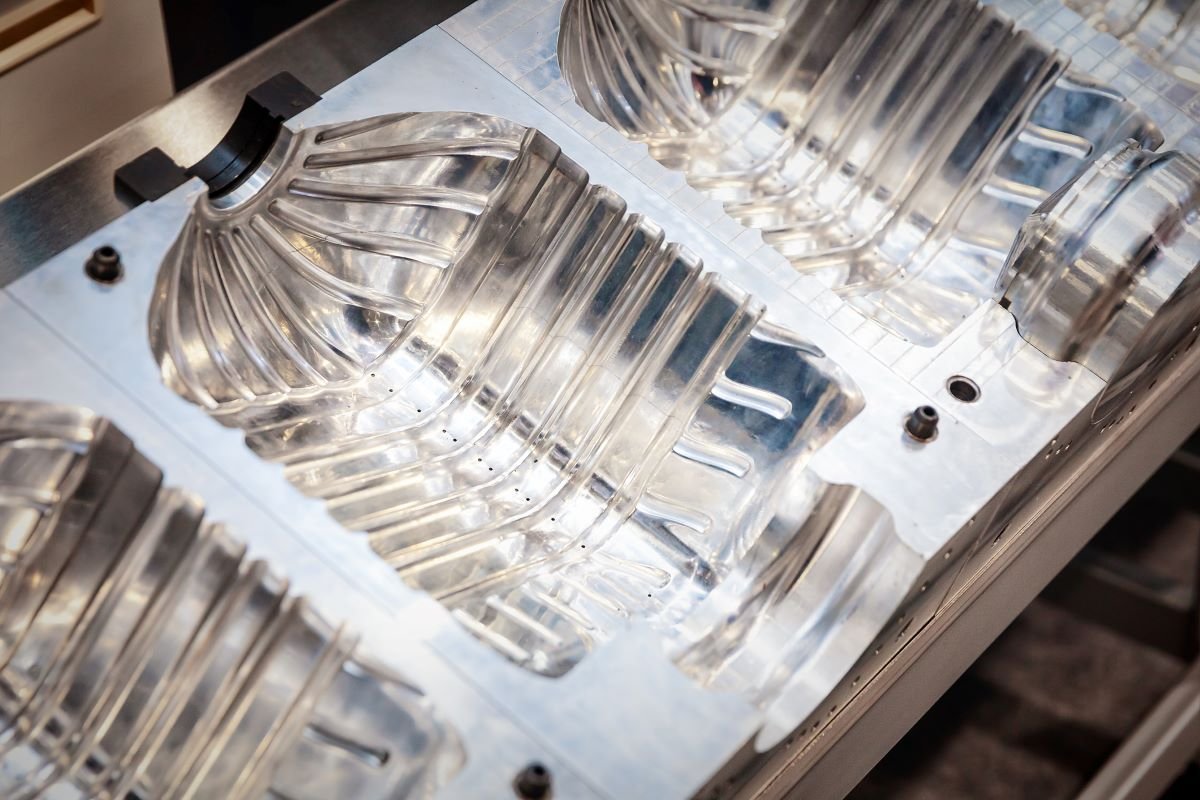
Key Takeaways
- Get a clear overview of Scope 1 and 2 emissions and their role in tracking a company’s carbon footprint.
- Understand why reducing them is key for achieving climate goals and regulatory compliance.
- See real-world examples across industries like manufacturing, aerospace, and automotive.
- Uncover common challenges companies face in cutting emissions.
- Discover seven practical ways to lower emissions, from energy efficiency upgrades to renewable energy adoption.
- Learn how Mavarick’s carbon accounting software simplifies emissions tracking and supports sustainability goals.
What are Scope 1, & Scope 2 Emissions?
Scope 1 emissions, known as direct emissions, are those greenhouse gases directly emitted by company-owned equipment, vehicles, or industrial processes. This is where the company has full command over its environmental output, whether that’s from burning fuel in production machinery or operating on-site boilers. Scope 2 emissions add another layer, capturing the indirect emissions generated by the energy a company buys—think electricity, steam, or cooling that’s essential for day-to-day operations but generated off-site. What’s unique about Scope 2 is that, while the emissions happen elsewhere, they’re still tied to the company’s energy demand. Together, Scope 1 and 2 emissions create a detailed picture of a company’s environmental influence, highlighting areas where strategic adjustments—like switching to renewable energy sources or optimising energy use—can drive measurable reductions. Scope 3 emissions take this framework even further, covering all other indirect emissions that occur along a company’s value chain. These include everything from the emissions generated by suppliers to those produced when customers use a product. Scope 3 often accounts for the largest share of a company’s total carbon footprint, making it a crucial area for companies aiming for comprehensive sustainability. For more insights into Scope 3 emissions and how to address them effectively, read our blog on scope 3 emissions and how to reduce it.
Why is There a Need to Reduce Scope 1 & 2 Emissions?
Did you know? Global energy-related CO₂ emissions hit a staggering 36.8 gigatonnes in 2022, a record that underscores the urgent need for stricter environmental laws. This surge in greenhouse gases directly fuels climate change, intensifying extreme weather events and disrupting ecosystems, which is why so many governments are enforcing stricter emissions standards. Scope 1 and Scope 2 emissions are especially concerning because they come from fossil fuel combustion and purchased energy—two major sources of CO₂ and other greenhouse gases. These emissions contribute heavily to air pollution, increase the risk of health issues for surrounding communities, and accelerate climate change. In high-emission industries like manufacturing, reducing Scope 1 and 2 emissions isn’t just a regulatory requirement; it’s a necessity for protecting the environment, ensuring public health, and meeting global sustainability goals. The greatest source of carbon emissions from automobiles throughout their lifetime comes from usage, which is categorised as scope 3 for a manufacturer. The emissions that result from usage dwarf those involved with production, but production emissions can still be significant. Fact Check The greatest sources of direct carbon emissions in the automobile manufacturing industry are from the transformation of materials. Materials transformation processes such as metal stamping, casing, forging and machining were found to generate 1,065 kg of CO2 for a generic 1532 kg vehicle. ena These direct carbon emissions would be reported under Scope 1 for the automotive industry.Challenges While Reducing Scope 1 & Scope 2 Emissions
- Upgrading Legacy Equipment: Older machinery and systems in manufacturing or industrial plants are often less efficient and emit more CO₂. Replacing or retrofitting these systems can be complex, time-consuming, and expensive.
- Energy Market Volatility: The cost of electricity, especially renewable energy, can fluctuate significantly. These price variations make it difficult to predict expenses and maintain a stable budget for Scope 2 emissions reduction.
- Lack of Real-Time Emissions Monitoring: Without real-time data collection tools, it’s challenging to get accurate, up-to-the-minute insights on energy use and emissions, which are essential for making timely adjustments and achieving reduction goals.
- Employee Training and Skill Gaps: Reducing emissions often involves adopting new technologies and practices, which may require specialised skills or additional training for employees, adding time and cost to the transition.
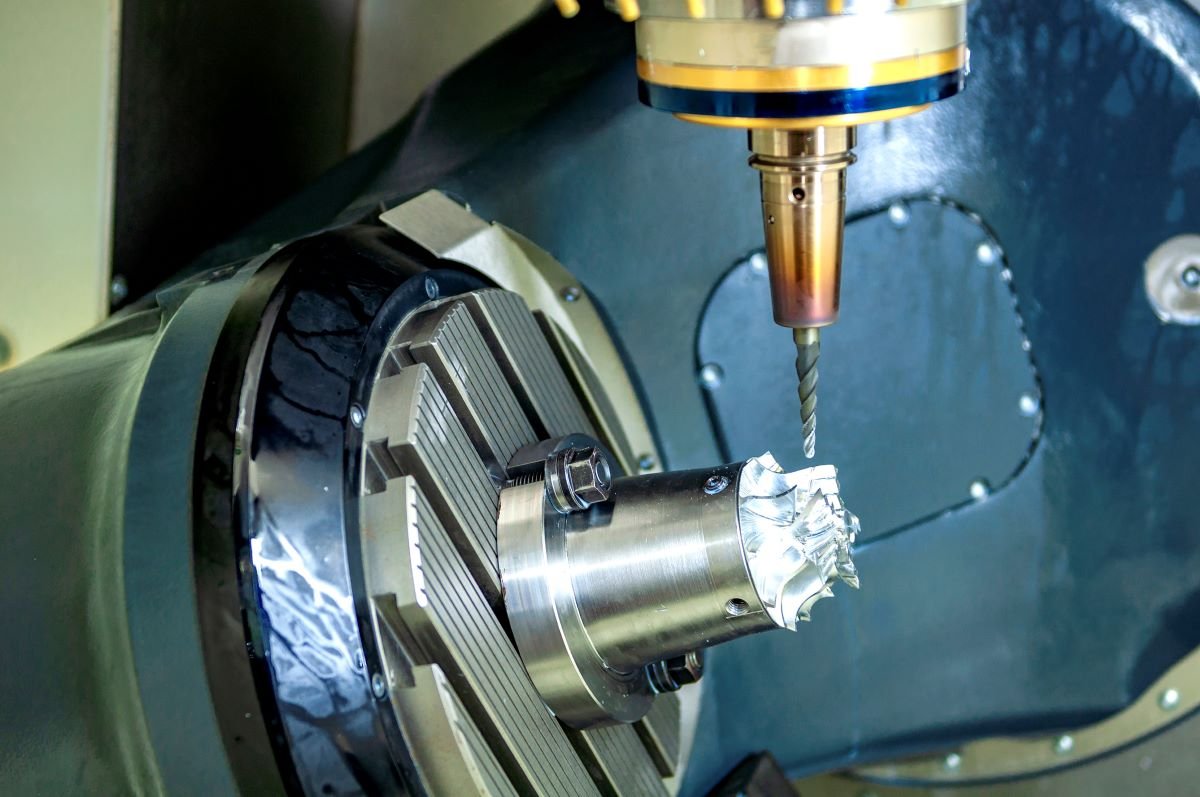
6 Ways to Reduce Scope 1 & 2 Emissions
1. Optimise Energy Efficiency in Operations
Conduct energy audits to identify and address inefficiencies in machinery, lighting, and HVAC systems. Simple adjustments, such as upgrading to LED lighting or installing variable-speed drives on equipment, can lead to immediate reductions in energy use and emissions.2. Switch to Renewable Energy Sources
Transition from traditional fossil fuels to renewable energy sources, such as solar, wind, or hydroelectric power, to cut Scope 2 emissions from purchased electricity. Many companies also invest in on-site renewable installations, which help reduce dependency on grid power.3. Implement Real-Time Emissions Monitoring and Reporting Software
Use advanced carbon reporting software to track emissions data in real-time and pinpoint high-emission areas. With tools like Mavarick’s carbon reporting platform, companies can streamline data collection, automate reports, and make targeted changes based on precise insights. Mavarick’s software ensures compliance while providing actionable insights, empowering companies to meet sustainability goals faster. To know more, check out our blog on the top 10 best carbon reporting software to know all about your options.4. Upgrade to Low-Emission Equipment and Vehicles
Replacing older, inefficient equipment and vehicles with energy-efficient or electric alternatives can significantly reduce Scope 1 emissions. This may include installing high-efficiency boilers, transitioning to electric or hybrid fleet vehicles, and adopting more efficient industrial processes.5. Enhance Process Efficiency
Reevaluate production processes to eliminate unnecessary steps, reduce idle times, and optimise the use of materials and energy. By streamlining operations, companies can cut down emissions at every stage, making the manufacturing process more sustainable and cost-effective.6. Engage Employees in Sustainability Initiatives
Educate and motivate employees to adopt low-emission practices in their daily roles. Whether it’s reducing energy consumption, minimising waste, or following optimised protocols, an informed workforce can be a valuable asset in achieving emissions reduction goals.Example of Scope 1 & Scope 2 Emissions in Manufacturing
Understanding Scope 1 and Scope 2 emissions is crucial for industries aiming to reduce their carbon footprint. Below are examples from various sectors, highlighting both types of emissions:1. Manufacturing Industry
Scope 1 Emission: Direct emissions occur through stationary combustion in manufacturing facilities. For example, fuel combustion in industrial boilers and furnaces generate high temperatures essential for processes like metal smelting or chemical synthesis. These emissions come from burning natural gas, coal, or oil, which releases CO₂ and other greenhouse gases directly into the atmosphere. Scope 2 Emission: Indirect emissions arise from purchased electricity needed to power machinery, production lines, and control systems. This electricity often comes from grid sources that may rely on fossil fuels. For instance, electronics manufacturers report that more than 50% of their CO₂ emissions are related to energy use in operations.2. Automotive Industry
Scope 1 Emission: Automotive manufacturing produces Scope 1 emissions primarily through surface coating and painting processes. These processes release greenhouse gases and VOCs as cars are painted and coated, which is essential for vehicle aesthetics and corrosion resistance but carries a high environmental impact. Scope 2 Emission: Scope 2 emissions stem from the electricity used in highly automated, robotic assembly lines responsible for welding, assembling, and finishing vehicles.3. Aerospace Industry
Scope 1 Emission: In aerospace manufacturing, Scope 1 emissions primarily arise from direct fuel combustion, particularly from jet fuel burned during prototype testing to verify safety and airworthiness, resulting in significant CO₂ output. Additionally, gas-fired boilers, furnaces, and heating systems, which are essential for facility operations in colder climates, contribute substantially to direct emissions by consuming large amounts of natural gas to maintain optimal indoor temperatures and support energy-intensive manufacturing processes. Scope 2 Emission: Scope 2 emissions in aerospace often involve indirect electricity usage across assembly lines and production systems. The extensive use of robotics and precision machines requires a stable, high-energy input.4. Medical Industry
Scope 1 Emission: Scope 1 emissions in medical manufacturing commonly arise from the use of sterilising agents like ethylene oxide (EtO) in medical device production and processing. This process is critical for sanitising equipment but releases volatile organic compounds (VOCs), a greenhouse gas with high global warming potential. Scope 2 Emission: Scope 2 emissions are largely tied to electricity usage in climate-controlled facilities required to maintain precision during medical device assembly. Cleanrooms that require strict temperature and humidity control consume considerable energy, resulting in indirect emissions from the grid. To know about scope 3 emissions in medical industry do read our blog on medical device manufacturer and scope 3 emissions. Siemens Healthineers estimates Scope 2 emissions contribute significantly to their operational footprint.5. Plastics Manufacturing
Scope 1 Emission: Plastic manufacturing often involves emissions from chemical reactions during polymerisation and curing. For example, CO₂ and methane can be released as byproducts of these reactions, making Scope 1 emissions particularly challenging to control without significant modifications to core chemical processes. Scope 2 Emission: The energy-intensive processes of extrusion and moulding in plastics manufacturing rely on indirect electricity, leading to significant Scope 2 emissions. These processes require high temperatures and extensive power use to maintain equipment at the necessary operational levels.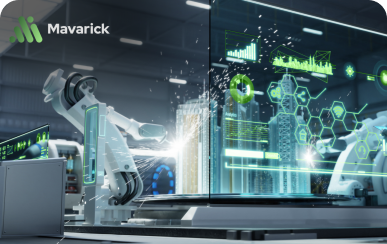
Laws Around Scope 1 and Scope 3 Emissions
Recent regulations have increasingly focused on Scope 1 and Scope 2 emissions to enhance corporate transparency and accountability in greenhouse gas (GHG) reporting. Notable developments include:1. European Union's Corporate Sustainability Reporting Directive (CSRD)
The CSRD, adopted in 2022, requires large companies and listed SMEs in the EU to disclose information on environmental, social, and governance (ESG) matters, including Scope 1 and Scope 2 emissions. The directive aims to standardise sustainability reporting across Europe, with phased implementation starting in 2024. For a deeper dive into this topic, check out our blog on CSRD regulations, where we cover comprehensive details and implications for businesses.2. U.S. Securities and Exchange Commission (SEC) Proposed Rule
In March 2022, the SEC proposed rules that would require publicly traded companies to disclose their Scope 1 and Scope 2 emissions, along with climate-related risks and their impacts on business operations. The proposal also includes certain Scope 3 emissions disclosures if they are material or included in the company's emissions targets.3. Ireland's Climate Action and Low Carbon Development (Amendment) Act 2021
Signed into law in July 2021, this act commits Ireland to a legally binding path to net-zero emissions no later than 2050, with an interim target of a 51% reduction in emissions by the end of this decade. The act provides the framework for Ireland to meet its international and EU climate commitments and to become a leader in addressing climate change.Bottom Line
Reducing Scope 1 and 2 emissions is both a regulatory necessity and a strategic opportunity for businesses to lower their environmental impact and boost efficiency. While each industry—from manufacturing to aerospace—faces unique challenges, targeted actions like adopting cleaner technology, enhancing data tracking, and shifting to renewable energy make a significant difference. By tackling Scope 1 and 2 emissions, companies position themselves as sustainability leaders, ready to meet the demands of consumers and stakeholders alike. Read our blog on ESG and its impact on sustainability for more information. Contact Mavarick today to understand the benefits of centralised carbon management and reporting tracking for your Scope 1, Scope 2 and Scope 3 emissions.Frequently Asked Questions (FAQs)
1, What are Scope 1 emissions? Scope 1 emissions are direct greenhouse gas emissions from sources that a company owns or controls, such as fuel combustion in company vehicles, boilers, and machinery. 2. What are Scope 2 emissions? Scope 2 emissions are indirect emissions from the energy a company purchases, like electricity, steam, heating, or cooling, which are consumed in day-to-day operations but produced off-site. 3. Why is it important to reduce Scope 1 and 2 emissions? Reducing Scope 1 and 2 emissions helps lower a company’s carbon footprint, supports compliance with environmental regulations, and aligns the business with global climate goals. 4. What are some challenges in reducing Scope 1 and 2 emissions? Challenges include the high costs of upgrading equipment, fluctuating energy prices, and the need for real-time data to accurately monitor and adjust emissions. 5. How can companies track Scope 1 and 2 emissions effectively? Companies can use carbon accounting software, such as Mavarick’s platform, to monitor emissions data in real-time, automate reports, and ensure regulatory compliance while identifying areas for improvement.Carbon Accounting System
Carbon Emissions Reporting for the Supply Chain
- Visible Supply Chain
- Quality Data You can Trust
- Auditable Reports