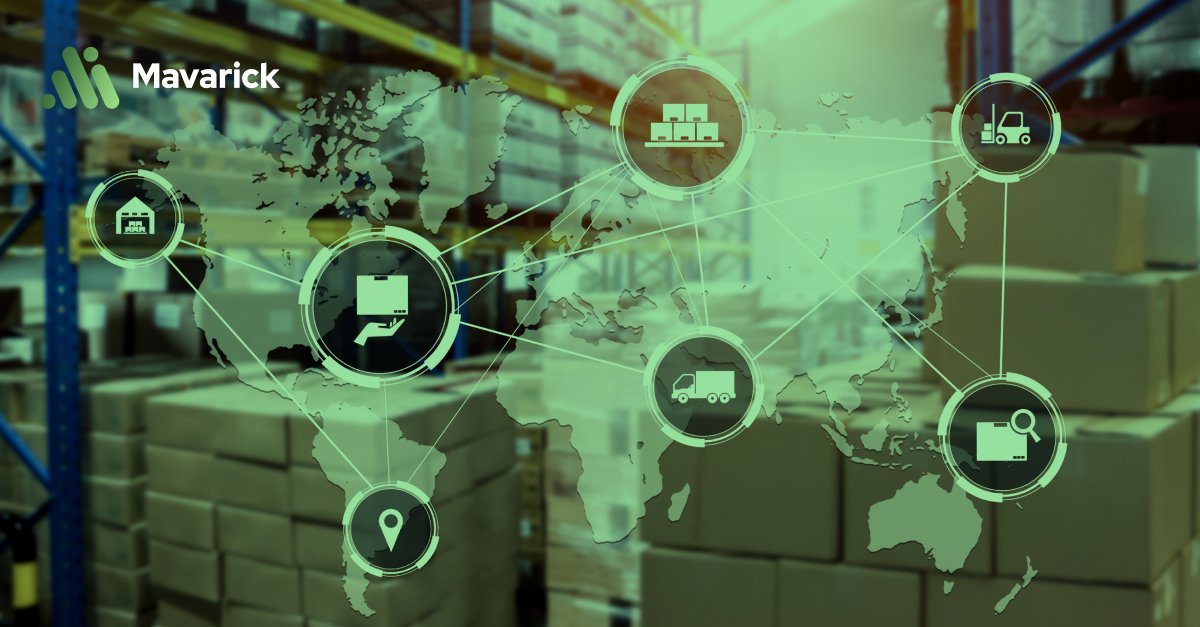
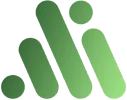
7 Powerful Strategies to Streamline Supply Chain in Manufacturing
Table of Contents
- Takeaways
- What is a Supply Chain in Manufacturing?
- Key Components of a Supply Chain in the Manufacturing Industry
- 7 Core Functions of a Supply Chain in Manufacturing
- 1. Procurement
- 2. Production Planning & Scheduling
- 3. Inventory Management
- 4. Logistics & Distribution
- 5. Quality Control
- 6. Demand Planning & Forecasting
- 7. Returns Management (Reverse Logistics)
- Common Challenges in Supply Chains in Manufacturing
- 1. Supply Disruptions Due to Geopolitical Events or Natural Disasters
- 2. Rising Costs of Raw Materials and Energy
- 3. Inefficiencies Caused by Manual Processes
- 4. Lack of Supply Chain Visibility and Real-Time Data
- The Power of Supply Chain Management in Driving Efficiency
- 1. Optimising Inventory with Real-Time Data
- 2. Streamlining Logistics Through Route Optimisation
- 3. Enhancing Transparency with Blockchain Technology
- 4. Strengthening Supplier Collaboration for Greater Agility
- 5. Driving Sustainability and Cost Savings Through Carbon Accounting
- The Role of Supply Chains in Manufacturing for Sustainability
- 1. Reducing Carbon Emissions and Waste
- 2. Responsible Sourcing and Ethical Practices
- 3. Compliance with Environmental Regulations
- Supply Chain 4.0 in Manufacturing: Unlocking Efficiency and Sustainability
- What is Supply Chain 4.0 in Manufacturing?
- Key Features of Supply Chain 4.0:
- The Impact of Supply Chain 4.0 in Manufacturing
- Future Trends of Supply Chain Management in Manufacturing
- 1. Adoption of Advanced Technologies
- 2. Supply Chain Regionalisation and Diversification
- Conclusion: The Future of Supply Chain in Manufacturing
- FAQs Supply Chain in Manufacturing
In the world of supply chain in manufacturing, efficient supply chain management (SCM) plays a vital role in reducing costs, optimising processes, and improving customer service. Supply chains are the critical link between raw materials and finished products, serving as the foundation of the manufacturing industry. They ensure seamless goods and services, helping manufacturers meet demand, maintain product quality, and deliver superior final products.
Fact Time
The global supply chain management (SCM) market was valued at USD 27.2 billion in 2022 and is expected to grow at a CAGR of 11.1% from 2023 to 2033, reaching an estimated value of USD 85.3 billion by the end of the forecast period.
The evolution of supply chain management in the manufacturing industry has been transformative—shifting from traditional, linear models to agile, tech-driven networks that embrace digital solutions and data analytics. Innovations like blockchain in supply chain management have revolutionised the sector by improving transparency, enhancing traceability, and reducing lead time, ultimately driving increased efficiencies and cost reductions.
The Carbon Connection:
Supply chains are directly linked to carbon emissions, especially in energy-intensive sectors like manufacturing. From sourcing raw materials to transportation, every stage of the global supply chain contributes to greenhouse gas (GHG) emissions. In fact, Scope 3 emissions—which include all indirect emissions from the supply chain—often represent the largest share of a company’s carbon footprint. This makes supply chain management a critical area for companies aiming to reduce their environmental impact and achieve net zero targets.
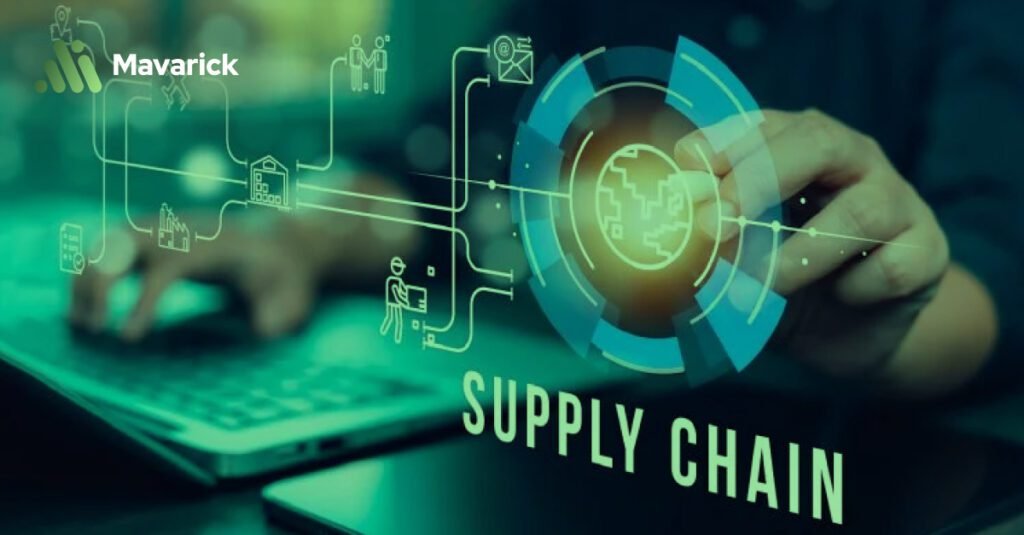
Did you know?
According to World Economic Forum, strategies like optimising inventory management, streamlining order fulfillment, and adopting blockchain technologies for transparent tracking can significantly lower emissions and promote sustainable supply chain practices
As the global supply chain grows more complex, businesses are increasingly adopting advanced supply chain management systems to stay competitive while addressing environmental concerns. Technologies like blockchain technologies offer unparalleled transparency and security, making it easier to manage the entire production cycle—from sourcing raw materials to order fulfillment—while minimising carbon footprints. Let's delve in;
Takeaways
- Boost Efficiency & Cut Costs: Use AI, IoT, and blockchain for optimized logistics, reduced waste, and lower operational costs.
- Track Carbon Emissions: Leverage carbon accounting tools to manage Scope 1, 2, & 3 emissions and meet CSRD & CBAM regulations.
- Enhance Visibility & Resilience: Real-time tracking and blockchain improve transparency and help manage supply chain risks.
- Strengthen Supplier Collaboration: Prioritize ethical sourcing and ESG compliance to build agile, responsible supply chains.
- Adopt Future-Ready Tech: Embrace Supply Chain 4.0, predictive analytics, and circular models for sustainable growth.
What is a Supply Chain in Manufacturing?
Supply chain in the manufacturing industry is the complete journey from sourcing raw materials through production, warehousing, and distribution, culminating in the delivery of final products to the end customer.
It involves transforming raw materials into finished products and delivering them to end customers. It is a complex network that coordinates the flow of goods and services, information, and finances across various stages of production, ensuring efficiency, cost-effectiveness, and high product quality.
Key Components of a Supply Chain in the Manufacturing Industry
- Suppliers: Responsible for providing essential raw materials, components, and parts required in the production process.
- Production Facilities: Where raw materials transform into finished goods through various manufacturing processes, ensuring product quality and efficiency.
- Warehousing & Distribution: Includes inventory management, storage, and logistics to streamline the flow of goods and optimise order fulfillment.
- End Customers: The final recipients of the products, whose satisfaction is crucial for sustained business success and improved customer service.
An effective manufacturing supply chain boosts operational efficiency, reduces costs, enhances lead time, and strengthens a company’s competitive edge within the global supply chain.
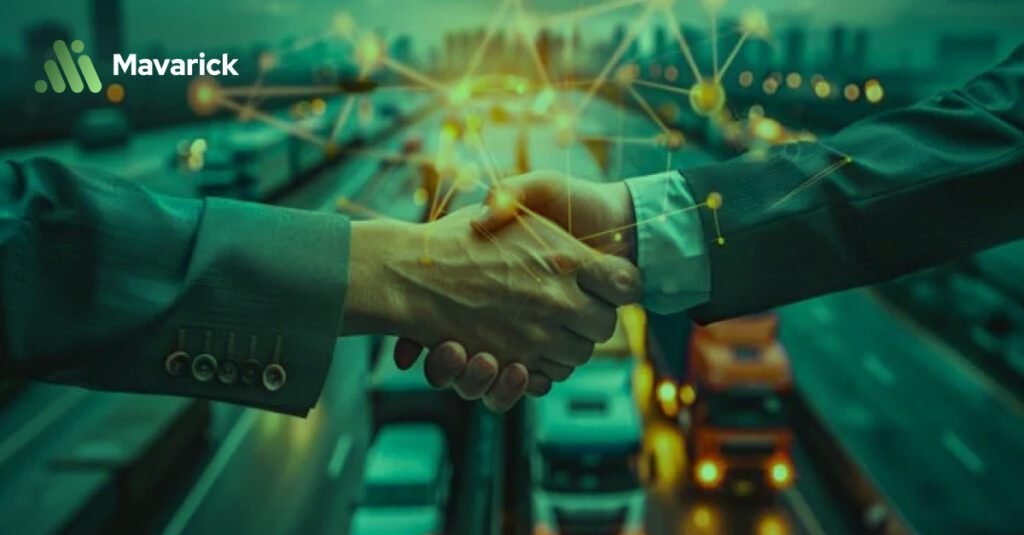
7 Core Functions of a Supply Chain in Manufacturing
A well-structured supply chain in manufacturing is essential for improving efficiency, reducing costs, and delivering high-quality final products to customers. While many associate supply chain management (SCM) primarily with logistics and transportation, it involves a range of interconnected functions that optimise the entire production process. Here’s an in-depth look at the 7 core functions of supply chain management:
1. Procurement
Definition: The process of sourcing and acquiring raw materials, components, and services needed for manufacturing.
Role in SCM: Efficient procurement ensures a steady supply of quality materials at the right time and price, directly affecting product quality and production timelines.
Best Practices:
- Establishing reliable supplier networks
- Negotiating favourable contracts
- Implementing sustainable procurement policies
2. Production Planning & Scheduling
Definition: Planning and managing production activities to ensure that manufacturing aligns with demand forecasts and resource availability.
Role in SCM: Strategic production planning optimises lead time, enhances the flow of goods, and ensures consistent product quality.
Best Practices:
- Demand forecasting and capacity planning
- Process optimisation for reduced waste
- Real-time monitoring of production workflows
3. Inventory Management
Definition: The practice of managing raw materials, work-in-progress, and finished goods to balance supply and demand efficiently.
Role in SCM: Efficient inventory management reduces storage costs, prevents stockouts or overstocking, and supports smooth order fulfillment.
Best Practices:
- Just-In-Time (JIT) inventory systems
- Real-time inventory tracking with IoT devices
- Safety stock strategies for demand fluctuations
4. Logistics & Distribution
Definition: Managing the transportation, warehousing, and distribution of goods across the global supply chain.
Role in SCM: This function ensures that goods move efficiently from suppliers to manufacturers and ultimately to end customers, optimising lead time and reducing transportation costs. Effective logistics and distribution strategies not only streamline operations but also play a significant role in minimising carbon emissions within the supply chain. Implementing sustainable logistics practices can help companies meet their environmental goals while improving overall efficiency.
As highlighted in blog on Supply Chain Emissions and Carbon Accounting Software, optimising logistics processes is essential for reducing a company's carbon footprint and enhancing transparency across the global supply chain.
Best Practices:
- Route optimisation to minimise fuel costs
- Integrated warehouse management systems
- Real-time shipment tracking for enhanced visibility
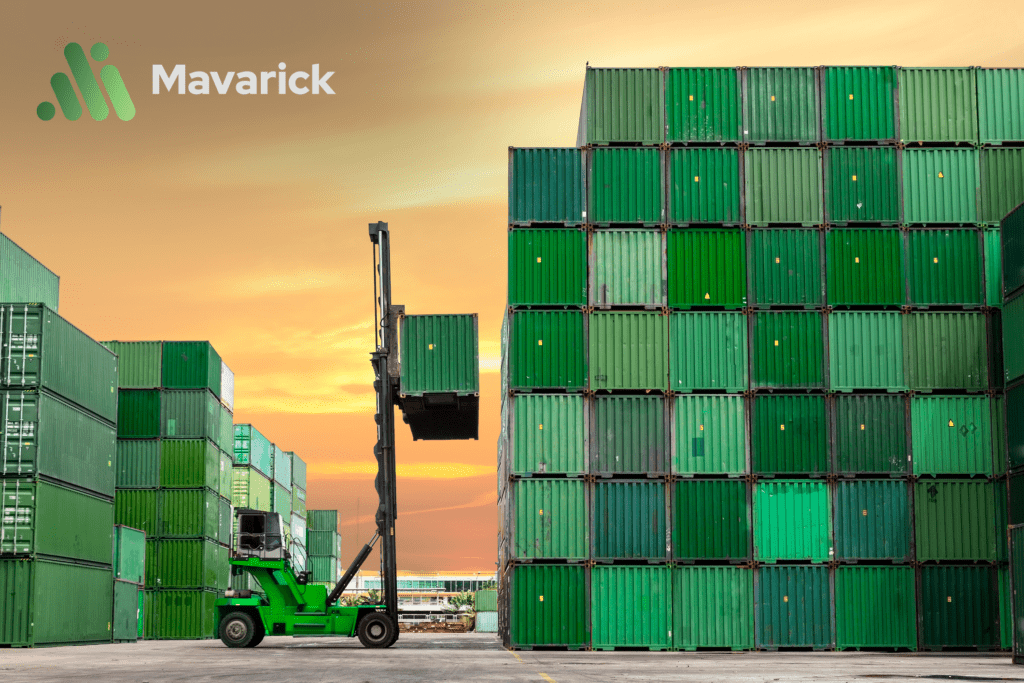
5. Quality Control
Definition: The process of maintaining quality by inspecting raw materials, monitoring the production process, and evaluating final products.
Role in SCM: Consistent product quality strengthens brand reputation, improves customer satisfaction, and reduces the cost of defects or recalls.
Best Practices:
- Regular quality audits and inspections
- Implementing Six Sigma and Total Quality Management (TQM)
- Continuous improvement strategies
6. Demand Planning & Forecasting
Definition: Predicting future customer demand to ensure the supply chain meets market needs without overproducing.
Role in SCM: Accurate demand planning helps manufacturers align production and inventory levels, reducing waste and improving responsiveness to market fluctuations.
Best Practices:
- Data-driven sales forecasting
- Integrating AI and machine learning for predictive analytics
- Collaboration between sales, marketing, and supply chain teams
7. Returns Management (Reverse Logistics)
Definition: Handling product returns, recycling, and disposal to recover value and minimise waste.
Role in SCM: Efficient returns management reduces losses from defective or unsold products while promoting sustainability through recycling and reuse.
Best Practices:
- Implementing flexible return policies
- Establishing repair and refurbishment programs
- Recycling initiatives for end-of-life products
For more insights into how modern supply chains can improve efficiency and sustainability, explore SAP’s guide to sustainable supply chains.
Common Challenges in Supply Chains in Manufacturing
Before we begin, did you know, that 71% of global companies highlight raw material costs as their number one supply chain threat for 2023?
Rising material prices, combined with global disruptions, are forcing manufacturers to rethink their supply chain management (SCM) strategies to remain competitive and resilient.
1. Supply Disruptions Due to Geopolitical Events or Natural Disasters
The global nature of modern supply chains makes them highly susceptible to external disruptions. Geopolitical tensions, trade wars, and natural disasters can cause significant delays, halt production, or even sever critical supply lines.
How to Mitigate
- Diversify supplier networks across different regions
- Implement risk management strategies and contingency planning
- Leverage real-time data for quick decision-making
2. Rising Costs of Raw Materials and Energy
Fluctuating costs of raw materials and energy remain a significant concern for manufacturers. Increased demand, supply shortages, and inflation have driven up prices, affecting the overall cost of goods sold (COGS).
Higher material and energy costs directly increase production expenses, leading to narrower profit margins. For energy-intensive industries, such as metal manufacturing or automotive, spikes in fuel prices can significantly raise transportation and operational costs.
How to Mitigate
- Adopt energy-efficient production processes (Explore strategies here)
- Negotiate long-term contracts with suppliers to lock in lower prices
- Invest in renewable energy sources to reduce dependency on volatile energy markets
3. Inefficiencies Caused by Manual Processes
Many manufacturing supply chains still rely on outdated, manual processes for tasks such as inventory management, order fulfillment, and quality control. These manual workflows often result in data silos, human errors, and slow decision-making.
How to Mitigate
- Implement automation tools and ERP systems to streamline processes
- Use blockchain technologies for real-time tracking and enhanced transparency
- Integrate AI and machine learning for predictive analytics
4. Lack of Supply Chain Visibility and Real-Time Data
One of the most critical challenges in modern supply chains is the lack of visibility across the entire network. Without real-time data on inventory levels, shipping status, and supplier performance, manufacturers struggle to make informed decisions.
How to Mitigate
- Adopt real-time tracking systems to monitor the flow of goods
- Use blockchain in supply chain management for end-to-end traceability
- Implement advanced data analytics for better forecasting and risk management

The Power of Supply Chain Management in Driving Efficiency
Efficient supply chain management (SCM) is crucial for streamlining operations, cutting costs, and enhancing product quality within the manufacturing industry. Modern supply chains, empowered by advanced technologies and data-driven strategies, do more than simply manage the flow of goods—they actively contribute to profitability, sustainability, and improved customer service.
1. Optimising Inventory with Real-Time Data
Modern inventory management systems utilise real-time data and predictive analytics to optimise stock levels, helping manufacturers balance supply and demand without the risks of overstocking or stockouts. This leads to reduced storage costs, minimised waste, and improved order fulfilment rates.
- Efficiency Boost: Real-time inventory tracking reduces manual errors and provides full visibility into stock levels across various facilities.
- Example: AI-powered demand forecasting enables manufacturers to predict sales trends more accurately and adjust inventory levels accordingly.
2. Streamlining Logistics Through Route Optimisation
Logistics and distribution play a pivotal role in ensuring a smooth flow of goods across the supply chain. Advanced logistics platforms now leverage AI and machine learning to optimise delivery routes, reduce fuel consumption, and lower transportation costs—all while improving lead time and enhancing customer satisfaction.
However, efficiency in logistics isn’t just about speed and cost—it’s also about sustainability.
This is where Mavarick steps in. While primarily known for its robust carbon accounting and supply chain emissions tracking,
- Mavarick empowers businesses to gain deeper visibility into the carbon impact of their logistics operations.
- By analysing real-time data across the supply chain, Mavarick.ai helps companies identify emission hotspots, streamline delivery routes, and choose more sustainable transportation options—ultimately reducing both costs and their environmental footprint.
For businesses looking to align logistics efficiency with sustainability goals, Mavarick offers the perfect balance between performance and environmental responsibility.
3. Enhancing Transparency with Blockchain Technology
Blockchain technology is revolutionising supply chain management by offering end-to-end transparency and traceability. In industries such as food, pharmaceuticals, and manufacturing, blockchain ensures every stage of the production process is accurately recorded, reducing the risk of counterfeit goods and ensuring compliance with regulations.
- Efficiency Boost: Blockchain reduces paperwork, eliminates fraud, and accelerates dispute resolution in complex supply chains.
- Supply Chain Visibility: Blockchain also enhances supply chain visibility by enabling real-time data sharing among stakeholders, leading to quicker decision-making and more agile responses to disruptions.
- Sustainability Impact: By improving traceability, blockchain helps manufacturers monitor and reduce their carbon footprint, making it easier to track Scope 3 emissions and meet sustainability goals.
4. Strengthening Supplier Collaboration for Greater Agility
Strong supplier relationships are essential for building agile and efficient supply chains. By fostering transparent communication and utilising shared data platforms, manufacturers can better coordinate with suppliers, reduce lead times, and quickly respond to market changes.
- Efficiency Boost: Collaborative planning with suppliers reduces production bottlenecks, enhances product quality, and supports the seamless flow of goods.
- Align Production Schedules: Shared demand forecasts enable suppliers to align their production schedules with manufacturer needs, preventing delays and improving supply chain efficiency.
5. Driving Sustainability and Cost Savings Through Carbon Accounting
Sustainability has become a key focus for modern supply chains. Manufacturers are now using carbon accounting software to monitor greenhouse gas (GHG) emissions across their global supply chains, helping them reduce their environmental footprint while cutting costs.
- Efficiency Boost: Tracking Scope 3 emissions—which include indirect emissions from suppliers and logistics—allows businesses to identify inefficiencies and implement greener, cost-effective practices.
- Improve Efficiency: Companies that adopt low-emission transport options and optimise delivery routes can reduce carbon output while improving operational efficiency.
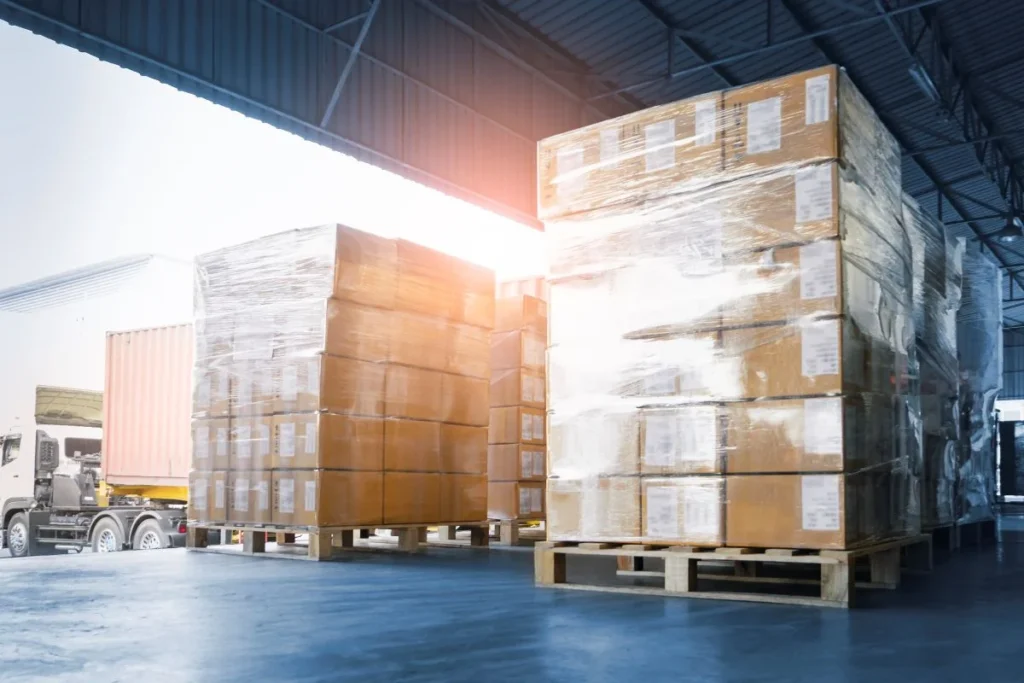
The Role of Supply Chains in Manufacturing for Sustainability
Sustainable manufacturing isn’t just about the production process—it’s about the entire supply chain. From raw material sourcing to final product delivery, every stage impacts a company’s carbon footprint and environmental responsibility. A well-optimised supply chain in manufacturing can significantly drive sustainability efforts while improving efficiency and reducing operational costs.
1. Reducing Carbon Emissions and Waste
Supply chains account for nearly 60% of global carbon emissions (McKinsey & Co.), making them a critical focus for sustainability initiatives. Manufacturers are increasingly turning to circular supply chain models that promote recycling, reuse, and waste reduction, shifting away from traditional linear supply chains.
- Circular Models:
These models aim to close the loop by recycling waste back into the production cycle, reducing raw material consumption and minimising landfill waste. - Carbon Accounting Software:
Real-time emissions tracking is now possible with advanced carbon accounting software, helping manufacturers pinpoint high-emission areas within their supply chain and implement reduction strategies. Platforms like Mavarick empower businesses to accurately measure, track, and report their Scope 3 emissions, ultimately reducing their environmental impact. - Sustainability Insight:
Companies that focus on supply chain optimisation can achieve significant carbon reductions and improve brand reputation by aligning with global sustainability goals.
2. Responsible Sourcing and Ethical Practices
Sustainable manufacturing starts with responsible sourcing. Ensuring that raw materials are ethically sourced not only supports ESG goals but also strengthens supply chain resilience.
- Ethical Sourcing:
Manufacturers are increasingly prioritising materials sourced from suppliers who follow fair labour practices, avoid environmentally harmful methods, and adhere to regulatory requirements. - Supplier Audits:
Regular supplier audits help maintain transparency, ensure compliance with environmental standards, and reduce the risk of unethical practices within the global supply chain. By leveraging blockchain technologies for traceability, companies can further guarantee that materials are sourced responsibly.
3. Compliance with Environmental Regulations
Navigating complex environmental regulations is one of the most pressing challenges in modern supply chain management. From global carbon taxes to industry-specific mandates, staying compliant is essential for manufacturers aiming to avoid costly penalties.
Key Regulations:
- EU’s Carbon Border Adjustment Mechanism (CBAM): Introduced to prevent carbon leakage and encourage greener manufacturing practices.
- Corporate Sustainability Reporting Directive (CSRD): Requires extensive disclosure of environmental and social impacts, with a strong emphasis on supply chain emissions.
Fact Check:
Non-compliance with the EU’s CBAM can result in fines of up to €50 per ton of unreported emissions (European Commission).
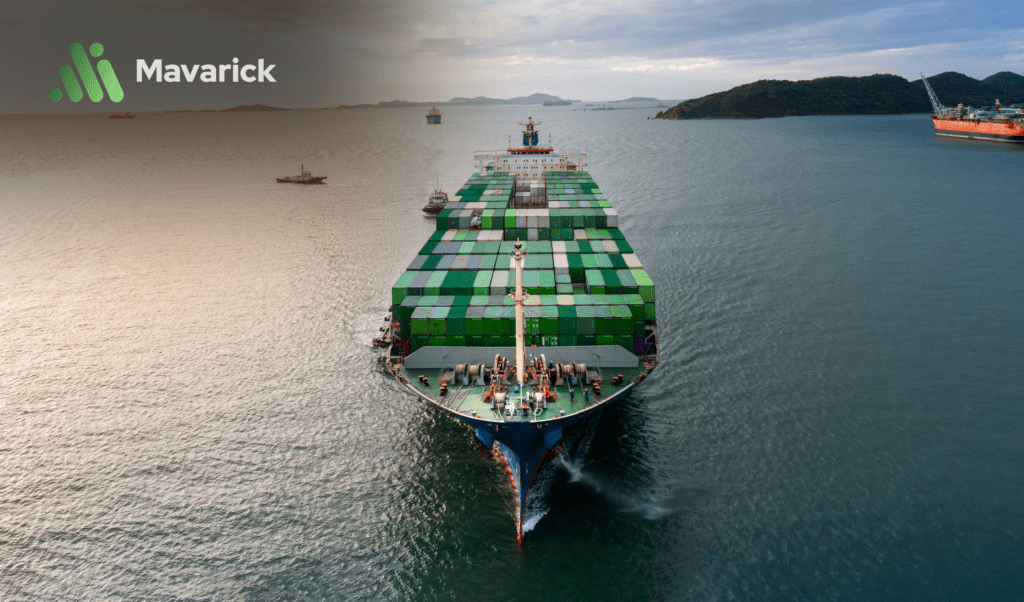
Supply Chain 4.0 in Manufacturing: Unlocking Efficiency and Sustainability
The rise of Industry 4.0 has revolutionised the traditional approach to supply chain management, giving birth to Supply Chain 4.0—a highly connected, agile, and data-driven ecosystem. This new era blends cutting-edge technologies like AI, IoT, Big Data, and blockchain to create smarter, faster, and more resilient supply chains.
What is Supply Chain 4.0 in Manufacturing?
Supply Chain 4.0 refers to the digital transformation of supply chains, where traditional linear models are replaced by integrated, real-time networks. By leveraging smart technologies, businesses can enhance efficiency, increase flexibility, and respond to market demands with greater agility.
Key Features of Supply Chain 4.0:
- Hyper-Connectivity with IoT:
Smart sensors, RFID tags, and connected devices allow real-time monitoring of inventory, shipments, and production processes, ensuring complete visibility across the global supply chain.
- Data-Driven Decision-Making with AI & Big Data:
AI and machine learning analyse vast amounts of data to forecast demand, optimise routes, and prevent disruptions. This predictive capability leads to reduced lead times, lower costs, and improved order fulfilment.
- Digital Twins for Scenario Planning:
Virtual replicas of supply chains—digital twins—enable businesses to simulate various production and distribution scenarios, helping to identify bottlenecks, optimise resources, and improve overall efficiency.
- Blockchain for Transparency & Security:
Blockchain technology enhances traceability and data security, ensuring transparent supply chains and reducing the risk of fraud. This is especially valuable in industries requiring strict compliance, such as pharmaceuticals and food manufacturing.
- Sustainability Integration:
Supply Chain 4.0 aligns with sustainability goals by tracking carbon emissions, minimising waste, and optimising energy consumption. With real-time carbon accounting software like Mavarick, businesses can measure and manage their Scope 3 emissions more effectively.
The Impact of Supply Chain 4.0 in Manufacturing
- Increased Efficiency: Automated processes and data-driven insights reduce operational costs and improve productivity.
- Enhanced Agility: Real-time data enables quick responses to market shifts and supply chain disruptions.
- Improved Sustainability: Advanced tracking and optimisation strategies reduce carbon footprints and support circular supply chain models.
- Stronger Resilience: Predictive analytics and scenario planning help companies anticipate risks and strengthen their supply chain’s adaptability.
Supply Chain 4.0 is not just a technological upgrade—it’s a strategic evolution that empowers businesses to be more resilient, sustainable, and competitive in a rapidly changing marketplace.
Future Trends of Supply Chain Management in Manufacturing
The manufacturing supply chain is undergoing significant transformations, driven by technological advancements, geopolitical shifts, and evolving market demands. Key trends shaping its future include:
1. Adoption of Advanced Technologies
- Artificial Intelligence (AI) and Automation: Manufacturers are increasingly integrating AI and automation to enhance efficiency and responsiveness. These technologies enable predictive analytics, real-time decision-making, and optimised inventory management, leading to more agile and resilient supply chains.
- 3D Printing (Additive Manufacturing): The use of 3D printing is expanding beyond prototyping to full-scale production, allowing for on-demand manufacturing and reduced lead times. This shift supports mass customisation and minimises the need for extensive inventory.
- Blockchain Technology: Blockchain enhances transparency and traceability within supply chains by providing secure, immutable records of transactions and product movements. This technology addresses issues related to trust and verification among stakeholders.
2. Supply Chain Regionalisation and Diversification
- Nearshoring and Friendshoring: In response to geopolitical tensions and supply chain vulnerabilities, companies are relocating manufacturing closer to end markets or to politically allied countries. This strategy reduces dependency on single regions and enhances supply chain resilience.
- Investment in Emerging Markets: Countries like India and Malaysia are becoming attractive manufacturing hubs due to their strategic locations and growing industrial capabilities. Global aerospace firms, for instance, are sourcing more components from India to mitigate Western supply chain disruptions.
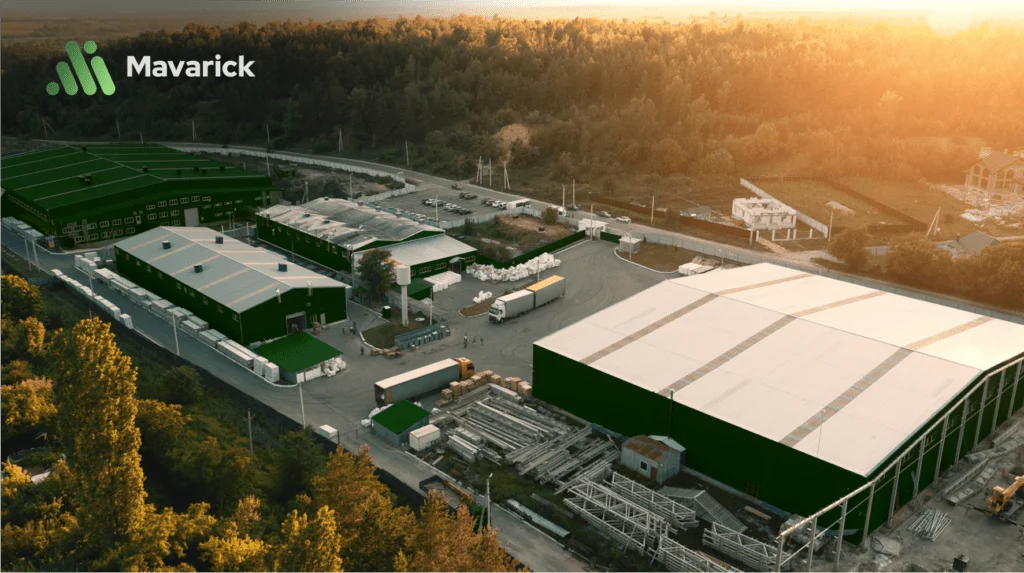
Conclusion: The Future of Supply Chain in Manufacturing
Supply chains are no longer back-end operations; they are critical engines of growth, efficiency, and sustainability. From foundational processes to advanced digital strategies, the power of supply chains in manufacturing lies in their ability to adapt, innovate, and drive competitive advantage.
The key question is: Will your supply chain power your growth or hold you back?
FAQs Supply Chain in Manufacturing
- What is Supply Chain 4.0 in Manufacturing?
Supply Chain 4.0 leverages technologies like AI, IoT, and blockchain to create smarter, more agile, and data-driven supply chains, improving efficiency and sustainability. - How Can Manufacturers Reduce Carbon Emissions in Supply Chains?
By using carbon accounting software, optimizing logistics, adopting energy-efficient practices, and tracking Scope 1, 2, and 3 emissions. - Why Is Supply Chain Visibility Important?
Real-time tracking and blockchain improve transparency, help manage risks, reduce delays, and support compliance with environmental regulations like CSRD and CBAM. - What Are the Key Challenges in Manufacturing Supply Chains?
Common challenges include supply disruptions, rising raw material costs, lack of real-time data, manual inefficiencies, and compliance with evolving regulations. - How Can Manufacturers Improve Supply Chain Efficiency?
Implementing AI-driven demand forecasting, real-time inventory tracking, route optimization, and automation tools can streamline operations and cut costs.
Carbon Accounting System
Carbon Emissions Reporting for the Supply Chain
- Visible Supply Chain
- Quality Data You can Trust
- Auditable Reports