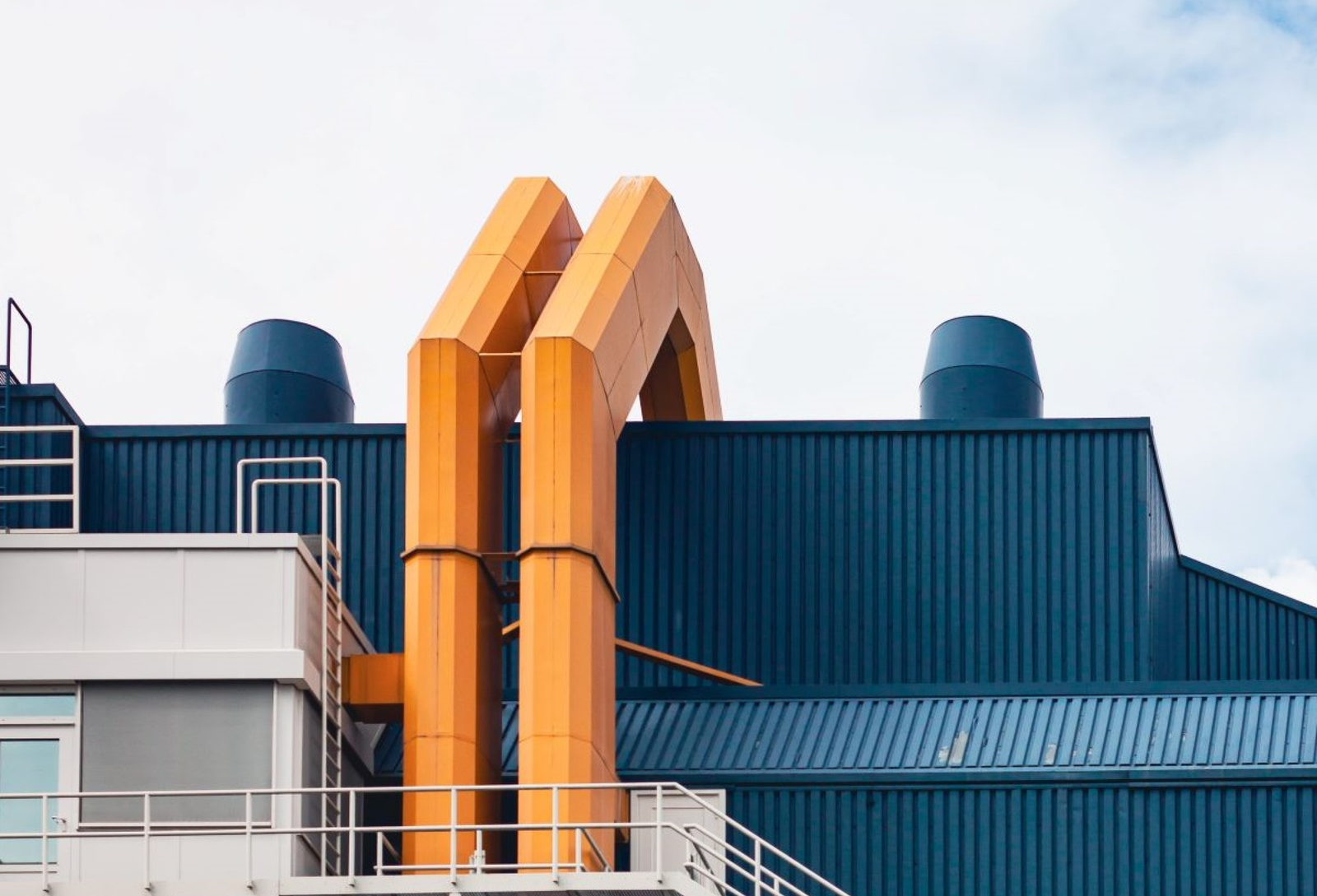
Table of Contents
- Understanding Energy Efficiency in Manufacturing Buildings
- Key Challenges to Energy Efficiency in Manufacturing Buildings
- Benefits of Improving Energy Efficiency
- Strategies for Enhancing Energy Efficiency in Manufacturing Buildings
- Innovations Driving Energy Efficiency
- Measuring and Monitoring Energy Efficiency
- The Future of Energy Efficiency in Manufacturing Buildings
- Conclusion
In the world of manufacturing, energy efficiency is no longer a mere option—it’s a strategic imperative. As energy costs soar and sustainability targets tighten, manufacturers are under pressure to do more with less. Optimising energy consumption not only reduces operational expenses but also aligns with global goals to minimise environmental impact. However, the focus often falls on production processes, overlooking a critical component of the equation: manufacturing buildings.
Manufacturing buildings are the backbone of industrial operations, housing equipment, employees, and systems that drive productivity. These facilities consume vast amounts of energy for lighting, heating, cooling, and powering machinery, making them hotspots for inefficiencies. Tackling energy waste in these structures isn’t just about compliance—it’s about gaining a competitive edge. Let’s delve into how manufacturers can transform their buildings into energy-efficient powerhouses while driving innovation and sustainability.
Understanding Energy Efficiency in Manufacturing Buildings
Energy efficiency in manufacturing buildings means reducing energy waste while maintaining or improving productivity. These buildings often consume enormous amounts of energy to power machinery, lighting, heating, ventilation, and air conditioning systems. Addressing inefficiencies in these areas can lead to dramatic cost savings and environmental benefits. For example, consider a typical manufacturing plant with outdated lighting systems and poorly insulated structures. These inefficiencies inflate energy bills and increase greenhouse gas (GHG) emissions. Learn more about implementing energy-efficient practices in manufacturing facilities here: Energy Management Systems - Complete Guide
Key Challenges to Energy Efficiency in Manufacturing Buildings
- Outdated Equipment: Legacy systems consume more energy and operate inefficiently.
- Lack of Expertise: Facility managers often lack knowledge about energy-efficient technologies.
- High Initial Costs: Upfront investment for retrofits and modern equipment can deter decision-makers.
- Regulatory Complexity: Navigating local and international energy efficiency standards can be challenging.
- Operational Disruptions: Implementing energy-saving measures might disrupt ongoing operations if not planned well.
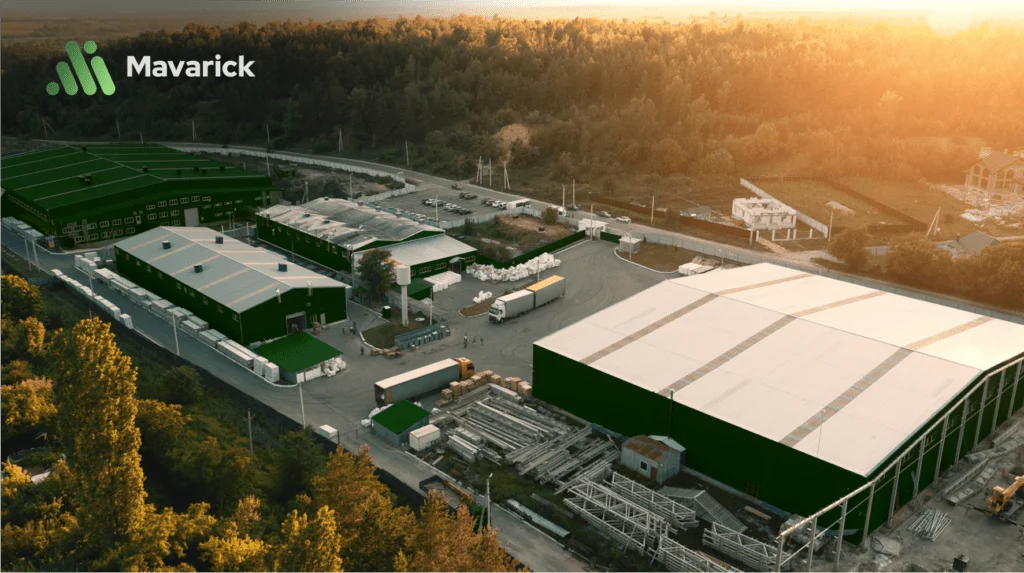
Benefits of Improving Energy Efficiency
- Economic Gains: Lower utility bills, reduced maintenance costs, and enhanced ROI.
- Environmental Impact: Decreased carbon footprint and contribution to global climate goals.
- Operational Advantages: Increased productivity, extended equipment lifespan, and reduced downtime.
Strategies for Enhancing Energy Efficiency in Manufacturing Buildings
- Conduct Energy Audits: An energy audit identifies inefficiencies and prioritises improvements. Auditors assess everything from machinery to building insulation, helping manufacturers make data-driven decisions.
- Invest in Energy-Saving Technologies:
- Lighting: Replace conventional bulbs with LED lighting systems.
- HVAC Systems: Opt for high-efficiency heating, ventilation, and cooling systems.
- Automation: Use smart sensors and IoT devices to optimise energy use.
- Implement Energy Management Systems (EMS): EMS tools monitor, track, and control energy consumption, providing actionable insights to optimise usage. Explore more about energy efficiency incentives for manufacturing industries here. Energy Efficiency Incentives and Policy in Manufacturing.
- Engage Employees: Educating staff about energy-saving practices fosters a culture of sustainability. Simple measures, like turning off equipment when not in use, can add up to significant savings.
Innovations Driving Energy Efficiency
- Smart Building Technologies: IoT-enabled devices and sensors optimise energy usage by monitoring real-time data and automating processes.
- Predictive Maintenance: AI-driven tools predict equipment failures, allowing timely interventions that reduce energy waste.
- Advanced Analytics: Data-driven insights help identify patterns and opportunities for energy optimisation.
Measuring and Monitoring Energy Efficiency
Key performance indicators (KPIs) such as energy intensity (energy consumed per unit of production) and carbon emissions per square metre of the building can help track progress. Tools like energy dashboards provide visual representations of consumption patterns, making it easier to identify and address inefficiencies. Additionally, frameworks like Streamlined Energy and Carbon Reporting (SECR) guide manufacturers in reporting energy usage and emissions, ensuring transparency and compliance. Discover the importance of data quality in energy monitoring here: Data Quality in Carbon Accounting.Overcoming Barriers to Implementation
- Financial Solutions: Governments and organisations offer grants, subsidies, and low-interest loans to offset initial costs.
- Training Programs: Upskilling employees ensures better utilisation of energy-efficient technologies.
- Regulatory Support: Staying updated on energy standards simplifies compliance and avoids penalties.
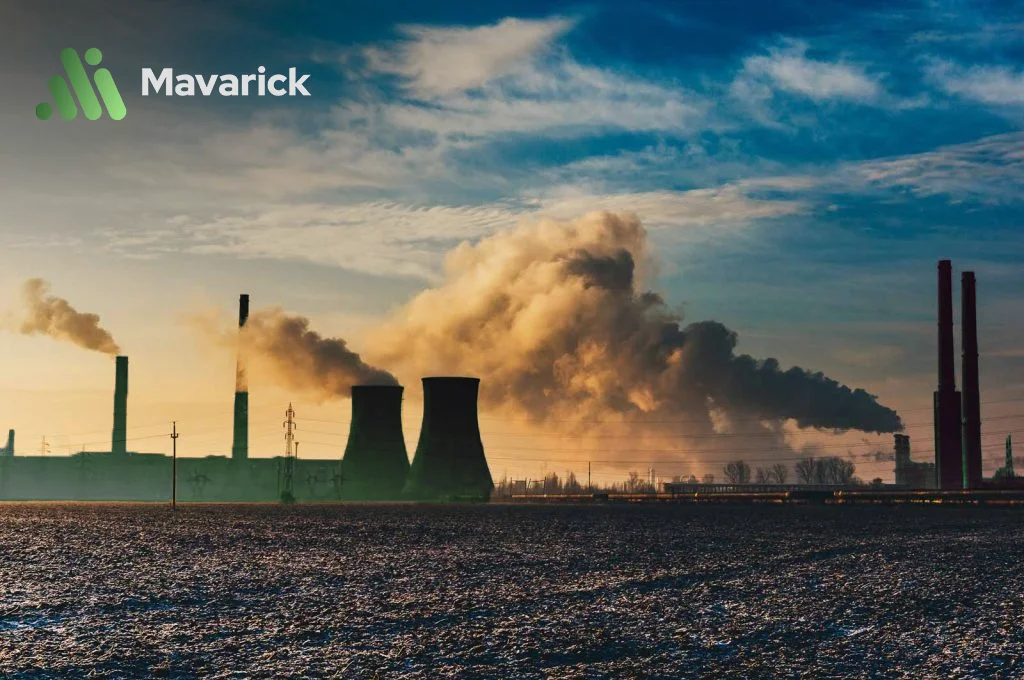
The Future of Energy Efficiency in Manufacturing Buildings
As technology evolves, energy efficiency will become even more integral to manufacturing. Emerging trends include:- Greater adoption of AI and machine learning for energy management.
- Increased use of renewable energy sources and microgrids.
- Enhanced collaboration between industry stakeholders to share best practices.
Conclusion
Energy efficiency in manufacturing buildings isn’t just about saving energy; it’s about driving innovation, cutting costs, and achieving sustainability goals. The opportunities are immense, from conducting energy audits to adopting smart technologies and renewable energy. By prioritising energy efficiency, manufacturers can unlock economic, environmental, and operational benefits while securing a competitive edge. Ready to take the next step? Contact Mavarick to transform your manufacturing operations into a model of energy efficiency and sustainability:Carbon Accounting System
Carbon Emissions Reporting for the Supply Chain
- Visible Supply Chain
- Quality Data You can Trust
- Auditable Reports