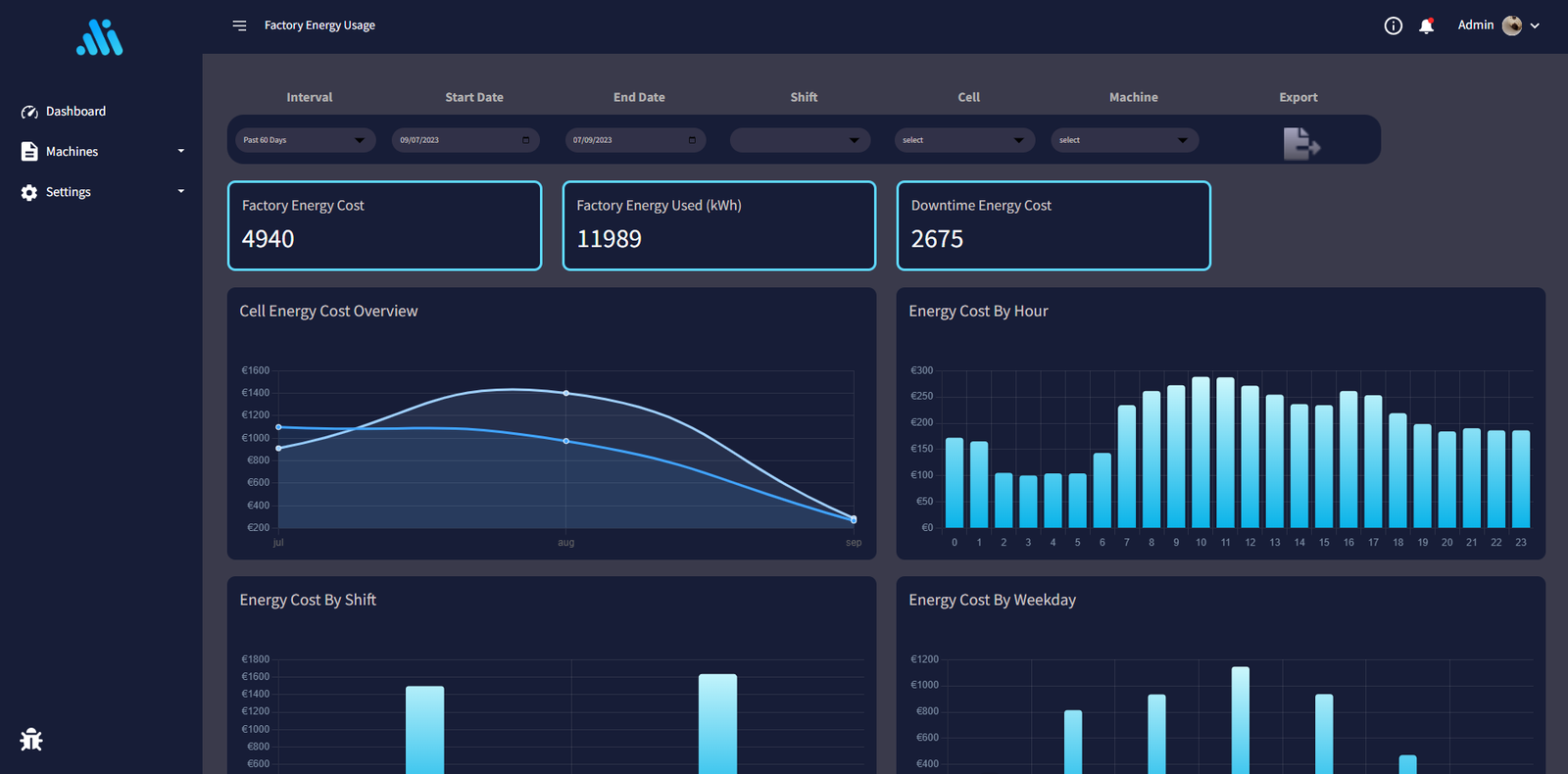
Table of Contents
- Key Takeaways
- What is Energy Efficiency in Manufacturing?
- Why is Energy Efficiency Important in Manufacturing?
- 1. Cost Savings and Competitiveness:
- 2. Environmental Impact Reduction:
- 3. Future-Proofing and Compliance:
- Role of Carbon Accounting in Driving Energy Efficiency
- How does Carbon Account Software help in Energy Efficiency in Manufacturing?
- 1. Comprehensive Data Collection and Analysis
- 2. Real-Time Monitoring and Reporting
- 3. Forecasting and Scenario Analysis
- 4. Regulatory Compliance and Benchmarking
- 5. Strategic Decision-Making
- 5 Key Challenges in Achieving Energy Efficiency in Manufacturing
- 1. Initial Investment Costs
- 2. Lack of Awareness and Expertise
- 3. Operational Disruptions
- 4. Resistance to Change
- 5. Data and Measurement Challenges
- 1. Conduct Comprehensive Energy Audits
- 2. Implement Energy Management Systems (EMS)
- 3. Upgrade to Energy-Efficient Equipment
- 4. Optimise Production Processes
- 5. Enhance Building Infrastructure
- 6. Utilise Renewable Energy Sources
- 7. Implement Waste Heat Recovery Systems
- Low Hanging Fruit - Where to Look for Energy Efficiencies in Manufacturing
- Buildings
- Lighting
- HVAC Systems
- Heating and Boilers
- KPIs of Energy Efficiency in Manufacturing
- 1. Energy Intensity (EI)
- 2. Energy Cost as a Percentage of Revenue
- 3. Specific Energy Consumption (SEC)
- 4. Carbon Intensity
- 5. Energy Savings Percentage
- 6. Energy Utilisation Rate (EUR)
- 7. Peak Energy Demand
- Energy Efficiency in Manufacturing Laws in EU
- Energy Efficiency Directive (EED) – Directive (EU) 2023/1791
- Ecodesign Directive – Directive 2009/125/EC
- Energy Labelling Regulation – Regulation (EU) 2017/1369
- Industrial Emissions Directive (IED) – Directive 2010/75/EU
- Renewable Energy Directive (RED II) – Directive (EU) 2018/2001
- Conclusion
- Frequently Asked Questions (FAQs)
- What is energy efficiency in manufacturing?
- How can energy management systems (EMS) help improve energy efficiency?
- What are some quick wins for improving energy efficiency in manufacturing?
- What challenges do manufacturers face in adopting energy efficiency measures?
- Are there regulatory requirements for energy efficiency in manufacturing?
Manufacturing is one of the most energy-intensive industries, yet it’s often riddled with inefficiencies that waste resources and inflate costs. Energy efficiency isn’t just about cutting utility bills; it’s about staying competitive, sustainable, and compliant in an increasingly demanding world.
Did you know that your factory might be consuming more energy than required, leading to unnecessary costs, wasted resources, and a larger environmental footprint?
Now imagine the impact of optimising energy use—reduced expenses, enhanced efficiency, and a more sustainable operation. Plus, you can also gain a comprehensive visibility into your supply chain emissions for a truly holistic approach to sustainability!
Fact Check
At the COP28 Summit in December 2023, 116 countries signed the Global Renewables and Energy Efficiency Pledge, committing to double the global average annual rate of energy efficiency improvements from around 2% to over 4% each year until 2030.
This initiative aims to significantly reduce energy consumption and greenhouse gas emissions worldwide. Gain access to accurate, reliable carbon emissions data you can trust for informed decision-making and impactful action.
In this guide, we’ll break down everything you need to know about improving energy efficiency in manufacturing, from quick wins to long-term strategies, and the technologies driving these changes.
Let’s dive deeper.
Key Takeaways
- Energy efficiency reduces costs, improves competitiveness, and ensures regulatory compliance in manufacturing.
- Upgrading equipment and using renewable energy are key strategies for reducing energy waste.
- Carbon accounting tools streamline emissions reporting, empower data-driven energy efficiency initiatives, and drive meaningful sustainability improvements.
- Overcoming challenges like high costs requires strategic investments and support.
- EU directives promote sustainable manufacturing through energy efficiency regulations.

What is Energy Efficiency in Manufacturing?
Energy efficiency in manufacturing is the practice of producing goods while optimising energy usage to minimise costs and environmental impact. It is more than just reducing energy consumption—it's about creating a streamlined, cost-effective, and sustainable operation.
Implementing Energy Management Systems (EMS) plays a pivotal role in achieving this by offering real-time monitoring, data analytics, and actionable insights to optimise energy use across facilities. Read more about energy management systems in our blog here.
However, while some countries accelerated their energy efficiency efforts in response to the global energy crisis, overall improvements in energy intensity have recently slowed, highlighting the need for more consistent global action.
To justify the comment, let's look at the stats below;
In 2023, global primary energy intensity—a key measure of energy efficiency—improved by approximately 1.3%, down from 2% in 2022 and below the 2010-2019 average of 1.9%.
This slowdown indicates that, despite some countries enhancing their energy efficiency efforts, overall global progress has decelerated, underscoring the need for more consistent and widespread action.
By focusing on reducing energy consumption and minimising energy waste, manufacturers can significantly reduce energy costs while unlocking opportunities for energy savings.

Why is Energy Efficiency Important in Manufacturing?
Energy efficiency in manufacturing is a critical driver of sustainability, cost reduction, and operational excellence in the manufacturing industry. As manufacturing facilities grow more energy intensive, focusing on energy saving measures brings significant benefits for businesses and the planet.
Did you Know?
The industrial energy efficiency market size is expected to reach US$ 41.2 Bn by 2030, from US$ 23.13 Bn in 2023, growing at a CAGR of 8.6% during the forecast period.
Here's why it matters:
1. Cost Savings and Competitiveness:
Reducing energy consumption directly cuts energy costs, enabling manufacturers to allocate resources to innovation and maintain competitive pricing.
2. Environmental Impact Reduction:
Manufacturing facilities are major contributors to greenhouse gas emissions. Energy efficiency minimises this environmental footprint by reducing waste and adopting cleaner energy sources.
3. Future-Proofing and Compliance:
With rising energy costs and stringent environmental regulations, energy efficiency ensures manufacturers remain compliant, resilient, and prepared for long-term sustainability challenges.
Energy efficiency in manufacturing isn't just about saving energy—it's a transformative strategy for building a sustainable and competitive industry.
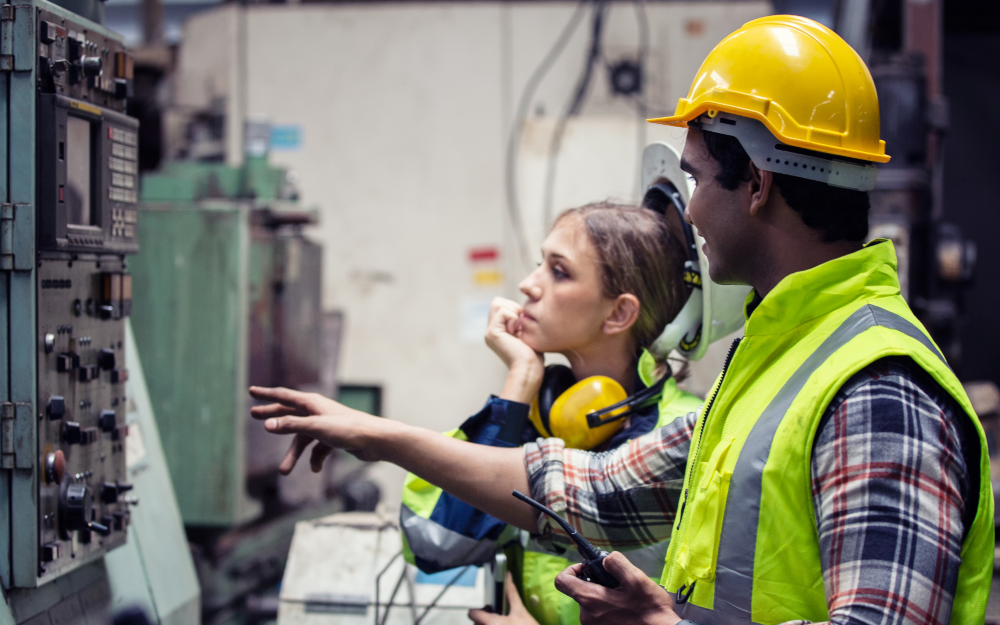
Role of Carbon Accounting in Driving Energy Efficiency
Carbon accounting is instrumental in enhancing energy efficiency within the manufacturing sector. By systematically measuring and analysing greenhouse gas (GHG) emissions, manufacturers can identify energy inefficiencies and implement targeted strategies to reduce both emissions and energy consumption. This dual approach not only aids in compliance but also promotes cost savings and environmental sustainability.
A study titled "Data-driven low-carbon transformation management for manufacturing enterprises: an eco-efficiency perspective" emphasises the importance of integrating carbon accounting with energy efficiency strategies in manufacturing.
The study underscores that a thorough understanding of carbon emissions across the production lifecycle is crucial for achieving significant energy efficiency improvements. By adopting data-driven strategies, manufacturers can effectively manage their low-carbon transformation, aligning operational goals with environmental objectives.
How does Carbon Account Software help in Energy Efficiency in Manufacturing?
Carbon accounting software plays a critical role in driving energy efficiency in manufacturing by offering precise insights into energy consumption and greenhouse gas (GHG) emissions. By digitising and streamlining the data collection process, manufacturers can identify inefficiencies, optimise resource utilisation, and align operations with sustainability goals. Here’s how:
1. Comprehensive Data Collection and Analysis
Carbon accounting software integrates energy usage data from various sources across the facility, creating a centralised system for monitoring. This holistic view enables manufacturers to pinpoint energy-intensive processes and identify areas for improvement.
2. Real-Time Monitoring and Reporting
Advanced software tracks energy consumption and emissions in real-time, offering actionable insights. This allows manufacturers to take immediate steps to reduce energy waste and meet efficiency benchmarks.
Solutions like Mavarick offer comprehensive features that ensure audit-ready data management, compliance with global standards such as the GHG Protocol, and streamlined auditor collaboration. By leveraging such tools, manufacturers can maintain data integrity, facilitate seamless verification processes, and uphold transparency in their climate reporting efforts.
3. Forecasting and Scenario Analysis
Using predictive analytics, carbon accounting software helps manufacturers model energy usage scenarios. This feature supports decision-making by demonstrating the potential impact of various energy efficiency measures before implementation.
4. Regulatory Compliance and Benchmarking
With automated compliance reporting, manufacturers can easily adhere to standards like ISO 50001 or the GHG Protocol. The software also enables benchmarking against industry standards, pushing for continuous energy improvements.
5. Strategic Decision-Making
Carbon accounting tools provide the data necessary to plan long-term energy efficiency strategies. Whether switching to renewable energy or optimising machine usage, informed decisions lead to significant energy savings.

5 Key Challenges in Achieving Energy Efficiency in Manufacturing
1. Initial Investment Costs
Energy-efficient technologies often require significant upfront capital, including the cost of new equipment, retrofitting existing systems, or implementing energy management software. Many manufacturers struggle to justify these expenditures despite the long-term cost savings.
2. Lack of Awareness and Expertise
Many organisations lack the technical knowledge or expertise to identify inefficiencies and implement effective energy-saving measures. This can lead to missed opportunities for reducing energy consumption and improving operations.
3. Operational Disruptions
Upgrading to energy-efficient systems or processes may require downtime, which manufacturers are often hesitant to accept due to potential impacts on productivity and revenue.
4. Resistance to Change
Cultural resistance within organisations can slow the adoption of energy-efficient practices. Employees and management may hesitate to change established workflows or invest in unfamiliar technologies.
5. Data and Measurement Challenges
Accurate tracking and analysis of energy consumption is critical for identifying inefficiencies, but many facilities lack the necessary tools or systems to collect and interpret energy data. Without reliable data, it’s challenging to implement targeted and effective energy efficiency measures.
Addressing these challenges requires a combination of education, strategic investments, and government or industry support through funding, training, and incentives.

Best Practices for Energy Efficiency in Manufacturing
Improving energy efficiency in manufacturing is essential for reducing operational costs, minimising environmental impact, and enhancing competitiveness. Below are key best practices that manufacturers can implement to achieve significant energy savings:
1. Conduct Comprehensive Energy Audits
- Identify Inefficiencies: Regular energy audits help pinpoint areas where energy is wasted.
- Set Baselines: Establish energy consumption baselines to measure improvements over time.
- Prioritise Actions: Focus on areas with the highest energy savings potential for immediate impact.
2. Implement Energy Management Systems (EMS)
- Real-Time Monitoring: Use EMS to track energy usage across all processes and equipment.
- Data Analytics: Analyse consumption patterns to identify trends and anomalies.
- Continuous Improvement: Set energy performance indicators and regularly review them to drive ongoing efficiency.
3. Upgrade to Energy-Efficient Equipment
- High-Efficiency Machinery: Invest in equipment with better energy ratings and lower consumption.
- Variable Speed Drives (VSDs): Install VSDs on motors to adjust energy use based on demand.
- Preventive Maintenance: Regularly maintain equipment to ensure optimal performance and energy use.
4. Optimise Production Processes
- Lean Manufacturing: Adopt lean principles to eliminate waste and improve process flow.
- Process Automation: Implement automation technologies to enhance precision and reduce energy waste.
- Energy-Efficient Scheduling: Schedule energy-intensive operations during off-peak hours to benefit from lower energy rates.
5. Enhance Building Infrastructure
- Insulation and Sealing: Improve insulation and seal leaks to reduce heating and cooling losses.
- Energy-Efficient Lighting: Replace traditional bulbs with LEDs and use motion sensors or timers.
- HVAC Optimisation: Upgrade HVAC systems and use smart thermostats for better climate control.
6. Utilise Renewable Energy Sources
- On-Site Generation: Install solar panels, wind turbines, or biomass generators to produce clean energy.
- Renewable Energy Contracts: Purchase green energy from utility providers if on-site generation isn't feasible.
7. Implement Waste Heat Recovery Systems
- Recapture Energy: Use waste heat recovery units to capture excess heat from processes and reuse it elsewhere in the facility.
- Combined Heat and Power (CHP): Consider CHP systems that simultaneously generate electricity and useful thermal energy.

Low Hanging Fruit - Where to Look for Energy Efficiencies in Manufacturing
All factories are different, and all factories use energy in different ways. However, some well-known areas of manufacturing processes consume large amounts of energy. Within these processes lie many low-hanging fruits for energy efficiency in manufacturing. Realising energy efficiencies in these low-hanging fruit will likely require some capital investment - though in many cases this can be minimal. Some of the places to find energy efficieciency
- Buildings
- Lighting
- Heating and Boilers
- HVAC Systems
- Buildings
Buildings
The buildings that house manufacturing operations can present huge opportunities for energy savings, depending on their age and condition. Building-related energy efficiencies typically involve heat regulation - heating, cooling, and ventilation. You can find efficiencies by ensuring that spaces are air-tight and well-insulated. Other places to look are in schedules for heating and cooling - ensuring that efforts to regulate heating closely follow schedules for building activity.
In Ireland, the SEAI handbook provides suggestions for finding building energy efficiency opportunities. You can find an even more comprehensive resource in CIBSE’s Guide F to Energy Efficiency in Buildings. For examples of low-hanging fruit to be found in your buildings see our post on How to Find Energy Efficiency in Manufacturing: Buildings
Lighting
Proper lighting is required in manufacturing operations to ensure safety and productivity. However, as lighting can represent up to 40% of a building’s electricity use, substantial savings can be found. The easiest way to enact large-scale energy efficiencies in lighting is to switch from traditional incandescent-bulb lighting to LED lights. By installing LED lighting, you can save 75% energy versus incandescent lighting. Another place that manufacturers can find energy savings from lighting is in the distribution of light within their operations.
Efficient distribution of light involves ensuring that you’re using the right amount of light in the right places. Often this boils down to ensuring that light sources are in physical proximity to crucial operations. Increasing the length of hanging lights, to bring them closer to operations, can enable manufacturers to deploy lower-energy bulbs.
Finally, a very simple way to ensure adherence to light-saving policies is to locate lighting controls in easy-to-reach places. Controls for lighting should be near to the operators that are utilising the lighting. For a more comprehensive guide to lighting in manufacturing, consult the SEAI Energy Efficient LED Lighting Guide.
HVAC Systems
Heating, ventilation, and air conditioning (HVAC) systems are primarily concerned with keeping conditions comfortable and productive for human operators. HVAC systems account for around 15% of all energy use in manufacturing and are thus a primary candidate for efficiency opportunities. HVAC systems can be complex to implement and operate, involving heating systems, fans, refrigerant compressors, and circulation pumps. While it is generally advisable to address HVAC systems within the scope of a professional energy audit, there are a handful of pedestrian opportunities to look into.
Something as simple as setting the correct time and date can help your HVAC system ensure that it is optimising temperatures for occupancy levels. Maintaining lower temperatures in hallways or pass-through areas can result in energy savings.
Restricting access to heating and cooling controls can also help to ensure that HVAC systems are operating at optimal levels. For a more comprehensive guide to HVAC energy efficiency opportunities, consult the SEAI Energy Audit Handbook.
Heating and Boilers
Oil and hot-water boiling systems are often used in manufacturing as sources for both space-heating and process-heating. Boilers are notorious culprits for energy inefficiencies. When looking to optimise energy efficiency in boilers, the three primary places to check are flue-gas exit temperatures, excess air in the system, and burnout.
Of course, you can gain substantial efficiencies by replacing an inefficient boiler. Condensing boilers are much more efficient at converting fuel to heat, and this efficiency can lead to 25% savings in energy costs for running the boiler.

KPIs of Energy Efficiency in Manufacturing
Key performance indicators (KPIs) in manufacturing have always revolved around cost, productivity, and quality, but today, energy efficiency is emerging as a crucial metric, redefining how success is measured in an increasingly sustainability-driven world.
1. Energy Intensity (EI)
This KPI measures the amount of energy consumed per unit of production. It helps assess the efficiency of energy use in manufacturing processes and identifies areas for improvement. A lower EI indicates higher energy efficiency.
2. Energy Cost as a Percentage of Revenue
This metric highlights the proportion of revenue spent on energy. It’s critical to understand how energy costs impact profitability and identify opportunities for cost reductions.
3. Specific Energy Consumption (SEC)
SEC measures energy consumption for specific products, processes, or machines, enabling manufacturers to target inefficiencies precisely.
4. Carbon Intensity
Carbon intensity tracks the amount of CO2 emissions generated per unit of production, helping manufacturers align with sustainability goals and carbon reduction targets.
5. Energy Savings Percentage
This KPI evaluates how much energy has been saved compared to a baseline period, reflecting the effectiveness of energy-saving initiatives.
6. Energy Utilisation Rate (EUR)
EUR measures how efficiently energy is being used compared to its availability. It helps identify whether energy resources are underutilised or wasted.
7. Peak Energy Demand
This KPI tracks the maximum energy demand during a specific period, helping manufacturers manage demand spikes and reduce peak charges. Managing peak demand improves energy efficiency and reduces overall costs.

Energy Efficiency in Manufacturing Laws in EU
The European Union (EU) has implemented several key directives to enhance energy efficiency within the manufacturing sector. These regulations aim to reduce energy consumption, lower greenhouse gas emissions, and promote sustainable industrial practices. Below are five pivotal EU laws focused on energy efficiency in manufacturing:
Energy Efficiency Directive (EED) – Directive (EU) 2023/1791
This directive establishes binding measures to help the EU achieve its energy efficiency targets, emphasising the 'energy efficiency first' principle. It aims for a reduction in EU final energy consumption by 11.7% by 2030 compared to projections based on the 2020 reference scenario.
Ecodesign Directive – Directive 2009/125/EC
This framework directive sets mandatory ecological requirements for energy-related products sold in the EU, aiming to improve their environmental performance throughout their lifecycle by integrating environmental aspects into product design.
Energy Labelling Regulation – Regulation (EU) 2017/1369
This regulation complements the Ecodesign Directive by requiring clear and consistent labelling of products to inform consumers about their energy consumption, thereby encouraging the production and purchase of more energy-efficient products.
Industrial Emissions Directive (IED) – Directive 2010/75/EU
The IED aims to reduce harmful industrial emissions across Europe through an integrated approach, setting principles for permitting and control of industrial installations to ensure operators apply Best Available Techniques (BAT) for high environmental protection, including energy efficiency.
Renewable Energy Directive (RED II) – Directive (EU) 2018/2001
This directive promotes the use of energy from renewable sources within the EU, setting binding targets for the overall share of renewable energy in the EU's energy consumption and encouraging the integration of renewables in industrial processes to enhance energy efficiency and reduce reliance on fossil fuels.
These directives collectively drive the EU's commitment to enhancing energy efficiency in manufacturing, fostering a more sustainable and competitive industrial sector.
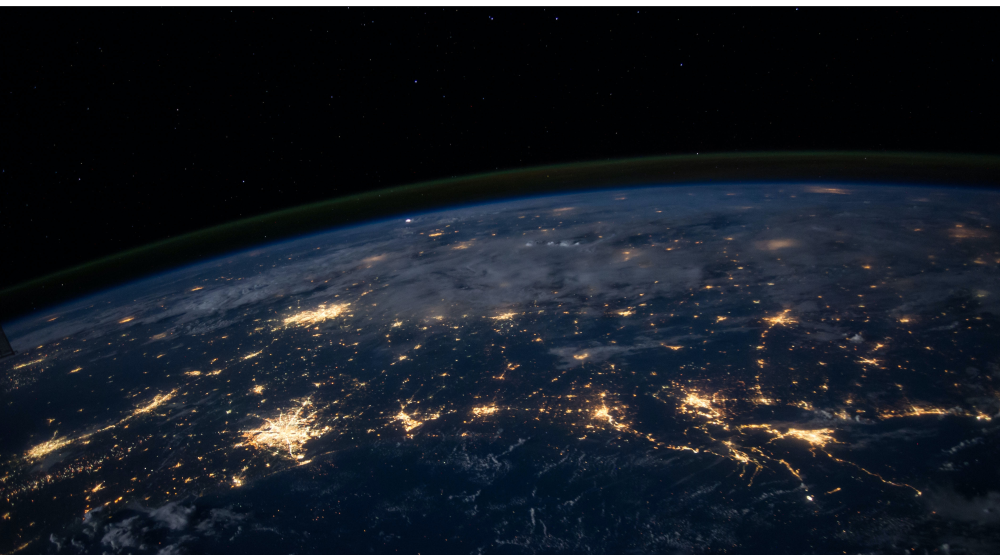
Conclusion
Energy efficiency is no longer just a cost-saving measure—it is the way to sustainable and competitive manufacturing. By leveraging advanced tools like carbon accounting software, manufacturers can uncover inefficiencies, make data-driven decisions, and achieve both operational and environmental goals.
As the global focus on reducing carbon emissions intensifies, adopting energy-efficient practices not only aligns your operations with evolving regulations but also strengthens your position as a leader in sustainability. With the right strategies and technologies, like those offered by Mavarick, manufacturers can confidently tackle the challenges of today while building a more energy-efficient and sustainable tomorrow.
Contact Mavarick today and take the first step toward a more energy-efficient future!
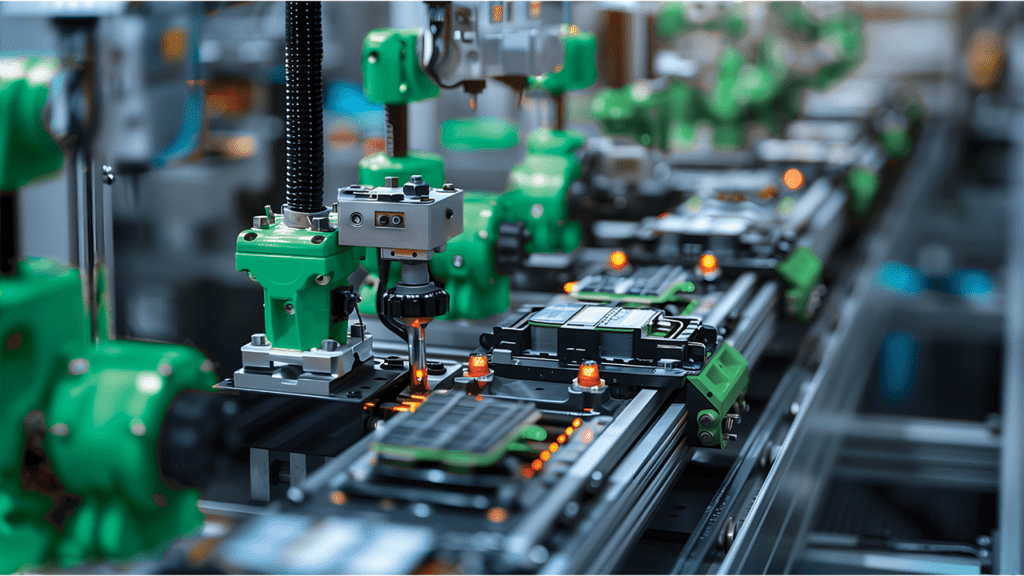
Frequently Asked Questions (FAQs)
What is energy efficiency in manufacturing?
Energy efficiency in manufacturing refers to the optimisation of energy usage to reduce waste, lower costs, and minimise environmental impact. It involves implementing technologies, systems, and practices that ensure energy is utilised effectively across all manufacturing processes.
How can energy management systems (EMS) help improve energy efficiency?
Energy management systems (EMS) enhance energy efficiency by providing real-time monitoring, analysing energy consumption patterns, and identifying areas of waste. They also facilitate predictive analytics, enabling manufacturers to plan energy-saving strategies and comply with global standards like ISO 50001.
What are some quick wins for improving energy efficiency in manufacturing?
Some quick wins include:
- Switching to LED lighting.
- Implementing energy-efficient scheduling for operations.
- Conducting regular energy audits.
- Upgrading outdated machinery to high-efficiency alternatives.
- Improving insulation and sealing leaks in building infrastructure.
What challenges do manufacturers face in adopting energy efficiency measures?
Key challenges include:
- High initial investment costs for energy-efficient technologies.
- Limited technical expertise or awareness of energy-saving opportunities.
- Resistance to change from employees or management.
- Operational disruptions during system upgrades.
- Difficulties in accurately tracking and measuring energy consumption.
Are there regulatory requirements for energy efficiency in manufacturing?
Yes, regulatory requirements such as the Energy Efficiency Directive (EED) in the EU mandate manufacturers to adopt energy-saving measures. Standards like ISO 50001 also provide frameworks for establishing energy management systems that ensure compliance with global energy efficiency goals.
Carbon Accounting System
Carbon Emissions Reporting for the Supply Chain
- Visible Supply Chain
- Quality Data You can Trust
- Auditable Reports