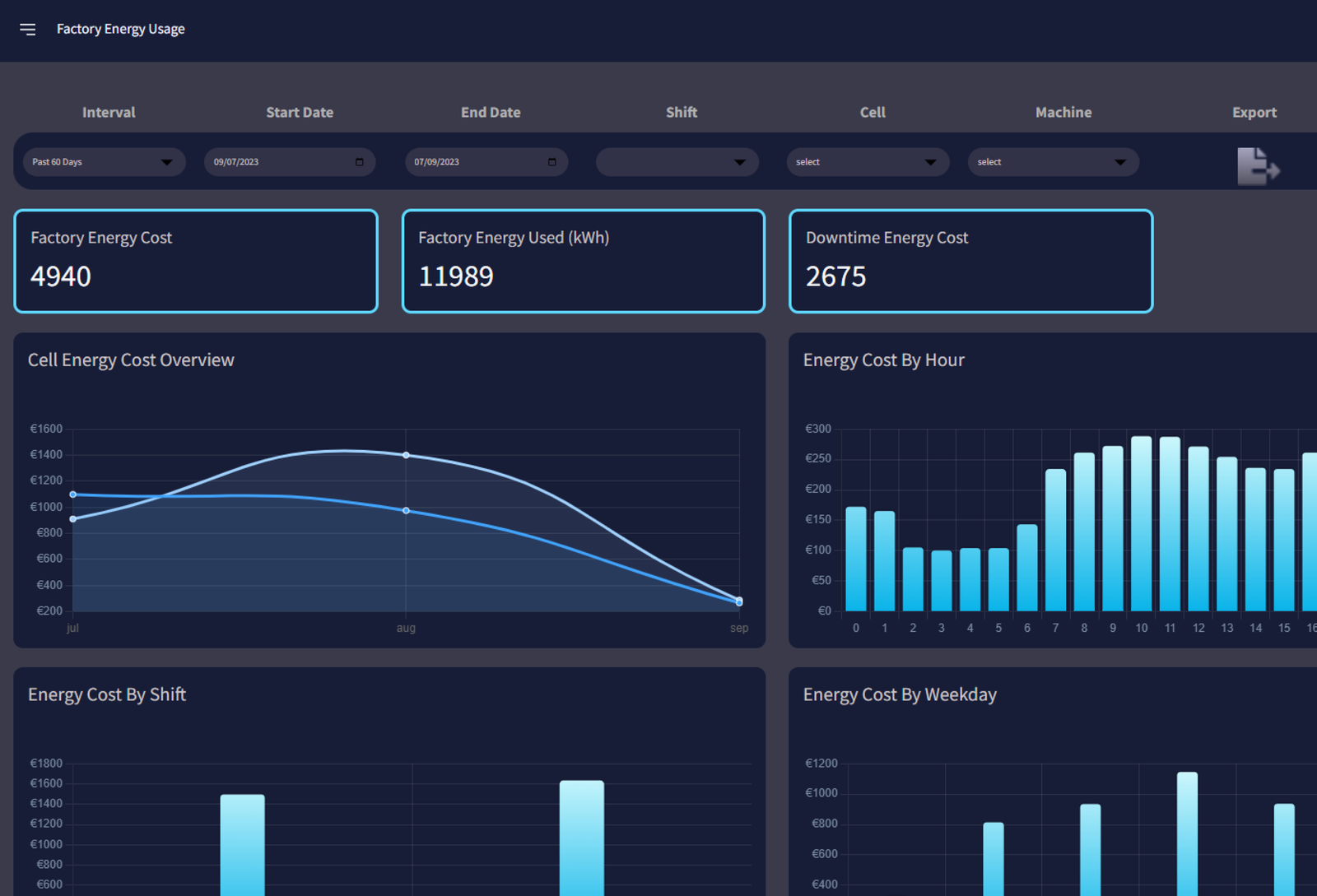
Table of Contents
- What is an Energy Audit in Manufacturing?
- Benefits of an Energy Audit in Manufacturing
- 1. Understand Energy Usage and Costs
- 2. Enhance Profitability
- 3. Prioritise Sustainable Operations
- 4. Mitigate Risks from Energy Cost Volatility
- 5. Uncover Wasted Energy
- 6. Identify Opportunities for Cost Reduction
- 7. Boost Operational Efficiency
- How Can Energy Audit Help Achieve Your Sustainability Goals?
- 1. Reduce Carbon Emissions
- 2. Enhance Energy Efficiency
- 3. Support Regulatory Compliance
- 4. Drive Long-Term Sustainability
- How to Prepare for Energy Audit in Manufacturing?
- What Happens During an Energy Audit?
- 1, Initial Consultation and Scope Definition
- 2. On-Site Assessment
- 3. Operational Context Gathering
- 4. Analysis of Energy Usage
- 5. Recommendations and Prioritisation
- 6. Financial and Sustainability Insights
- 7. Strategic Decision-Making Tool
- 8. Follow-Up and Monitoring (Optional)
- What is Assessed in a Energy Audit for Manufacturing?
- Physical State, Function and Energy Usage
- What is an Energy Audit Report?
- How to Fund an Energy Audit?
- Bottomline
- FAQs About Energy Audits in Manufacturing
An energy audit in manufacturing isn’t just a routine check; it’s a game-changer. It identifies opportunities to optimise energy usage, reduce energy consumption, and slash those utility bills.
Imagine this: your manufacturing facility is running at full throttle, but behind the scenes, energy is slipping through the cracks. From skyrocketing energy bills to wasted energy in outdated processes, inefficiencies might be quietly draining your resources. But here’s the good news—an energy audit can turn things around!
Whether it's fine-tuning your air conditioning systems, addressing industrial energy waste, or uncovering cost-saving measures, an energy audit brings clarity to your energy costs and unlocks significant savings. Ready to transform your carbon footprint into a success story? Let’s dive in!
Takeaways
Let's take a look at the topics that this guide will help you to understand
- What is an Energy Audit in Manufacturing?
- Benefits of Energy Auditing
- Energy Audit and Sustainability Goals
- How to prepare for an Energy Audit?
- What is Assessed in an Energy Audit for Manufacturing?
- What does an energy audit report look like, and how do I use it?
- Where to find government resources to help fund an Energy Audit
- Find a Qualified Auditor – Identify a certified energy auditor with expertise in manufacturing. For example, in Ireland, the SEAI website lists registered auditors.
- Define the Audit Scope – Decide which areas or systems (e.g., air conditioning, machinery) the audit will cover.
- Collect Key Data – Prepare utility bills, maintenance records, and production schedules to assist the auditor.
- Inform Your Team – Brief your staff about the audit and assign a point of contact to collaborate with the auditor.
- Prepare the Site – Ensure all equipment and areas are accessible for inspection during the audit.
- Pre-Audit: Steps the manufacturer & the auditor take prior to conducting the site visit
- Conducting the site visit
- Analysing the audit’s findings and providing recommendations
- The auditor meets with the manufacturer to understand the facility’s operations, goals, and challenges.
- Together, they define the scope of the audit, identifying key areas, equipment, or processes to be assessed.
- A professional energy auditor visits the manufacturing facility to conduct a detailed inspection.
- The auditor evaluates energy-intensive areas such as shop floors, cells, machinery, HVAC systems (e.g., air conditioning), lighting, and production processes.
- Measurements are taken for parameters like energy flow, utility bills, and equipment efficiency to determine energy usage patterns.
- The auditor collaborates with the facility’s management and staff to gain insights into operational practices and energy demand cycles.
- This step ensures that recommendations are practical and aligned with the facility's unique requirements.
- Data collected from the site is analysed to identify inefficiencies, wasted energy, and areas of potential improvement.
- Benchmarking against industry standards helps determine where the facility stands in terms of energy costs and carbon footprint.
- The auditor provides a detailed report with a prioritised list of energy-saving measures, supported by financial impact calculations.
- Recommendations may include upgrading to more efficient equipment, improving insulation, optimising production schedules, or switching to renewable energy sources.
- The report includes cost-benefit analyses, showing how each recommendation affects energy bills, operational costs, and long-term savings.
- Sustainability benefits, like reductions in carbon emissions and alignment with environmental goals, are also highlighted.
- The audit report becomes a valuable resource for future planning, helping manufacturers make informed capital investment decisions.
- It serves as a reference point for tracking progress, implementing energy-efficient technologies, and reassessing performance over time.
- Some audits include follow-up services to help manufacturers implement recommended actions and monitor their effectiveness.
- Building
- Lighting
- Heating and boilers
- Production machinery
- Pumps
- Transport fleet, telematics
- Refrigeration
- Industrial processes
- Wastewater treatment
- Compressed air
- Physical state, function and energy usage
- Opportunities to save energy
- Major risks
- Heat pumps are properly recovering energy from cooling loads
- Excessive air leakage in ovens, furnaces or extraction systems
- Production machine rated at 16KW and is in fact consuming at that rate during production run
- Energy Usage Analysis – A breakdown of how energy is consumed across systems, such as machinery, lighting, and air conditioning.
- Identified Inefficiencies – Highlights areas of wasted energy and potential improvements.
- Recommendations – A prioritised list of energy-saving measures, often supported by cost-benefit analyses.
- Financial Impact – Estimates of cost savings, utility bill reductions, and potential capital investment requirements.
- Sustainability Insights – Projections on how suggested actions will reduce carbon emissions and align with sustainability goals.
- Government Grants: Many governments provide financial assistance to cover the costs of energy audits. These grants are often aimed at encouraging businesses to enhance their energy efficiency and sustainability practices.
- Tax Incentives: Countries like the US offer tax benefits for energy-efficient upgrades. For instance, the Commercial Energy Efficiency Tax Deduction allows US manufacturers to deduct $5 per square foot of retrofitted shop space that improves energy performance.
- Utility Rebates: Some energy providers offer rebates or financial support for businesses conducting energy audits, particularly in industrial and energy-intensive sectors.

What is an Energy Audit in Manufacturing?
An energy audit is a comprehensive assessment of energy usage within a facility, designed to identify inefficiencies, evaluate energy consumption patterns, and recommend actionable solutions to reduce waste and save energy.
Think of it as a diagnostic tool that uncovers where and how energy is being consumed, whether it's through lighting, heating, cooling, or production processes. The goal is to enhance energy efficiency, lower energy bills, and ultimately minimise the carbon footprint of a business.
During an energy audit, professionals—commonly referred to as energy auditors—evaluate energy sources, analyse utility bills, and provide insights into cost-saving opportunities. This process not only helps businesses achieve significant energy savings but also contributes to sustainability goals by reducing environmental impact.
Benefits of an Energy Audit in Manufacturing
An energy audit of your manufacturing shop floor offers invaluable insights into your operations, helping you take control of your energy consumption, energy costs, and their impact on overall profitability. By identifying inefficiencies and opportunities for improvement, an energy audit in manufacturing sets the stage for more energy-efficient and sustainable operations.
Here’s how an energy audit can benefit your business:
1. Understand Energy Usage and Costs
Gain a clear picture of how energy is being used across your manufacturing processes. This knowledge empowers you to tackle excessive energy usage, reduce energy bills, and achieve significant cost savings.
2. Enhance Profitability
By uncovering hidden inefficiencies and implementing energy-saving measures, you can lower operational expenses and boost profitability—without compromising productivity.
3. Prioritise Sustainable Operations
An energy audit helps you set realistic goals for reducing your carbon footprint and improving energy efficiency, aligning your operations with modern sustainability standards.
4. Mitigate Risks from Energy Cost Volatility
The audit provides a roadmap to navigate fluctuations in utility bills and volatile energy markets, giving you strategies to stabilise costs and manage risks effectively.
5. Uncover Wasted Energy
From inefficient machinery to poor HVAC performance (like outdated air conditioning), an energy audit pinpoints where wasted energy occurs, offering targeted solutions to minimise losses.
6. Identify Opportunities for Cost Reduction
Whether it’s through upgrading equipment, optimising processes, or switching to better energy sources, the audit highlights areas for cost-efficient improvements across your industrial energy systems.
7. Boost Operational Efficiency
By addressing inefficiencies and improving business energy practices, an energy audit enhances the overall performance of your manufacturing floor.
How Can Energy Audit Help Achieve Your Sustainability Goals?
Every kilowatt-hour saved is a step closer to a sustainable future. But have you ever thought about how an energy audit bridges the gap between managing carbon emissions and achieving sustainability goals?
It’s more than just identifying areas of energy savings—it’s about transforming how businesses think about their energy consumption and its environmental impact. To achieve a business's sustainability goals, energy audit can;
1. Reduce Carbon Emissions
By identifying and addressing inefficiencies, an energy audit lowers energy consumption, directly reducing your facility’s carbon footprint and aligning with global sustainability efforts like the Paris Agreement.
2. Enhance Energy Efficiency
The audit pinpoints areas of wasted energy and provides actionable solutions, such as upgrading equipment or optimising processes, to maximise energy savings and minimise environmental impact.
3. Support Regulatory Compliance
Energy audits help businesses meet stricter environmental regulations by ensuring their operations adhere to sustainability standards and reduce greenhouse gas emissions.
4. Drive Long-Term Sustainability
With a clear roadmap for cost reduction and energy optimisation, manufacturers can invest in sustainable practices, positioning themselves as leaders in eco-conscious operations while achieving measurable progress toward their sustainability goals.
Mavarick can further amplify these benefits by providing cutting-edge tools that streamline energy audits and sustainability reporting. With features like real-time energy tracking, data automation, and actionable insights tailored for manufacturing, Mavarick empowers businesses to make smarter decisions for reducing energy waste and emissions.
Learn more about our energy auditing solutions that can help your facility achieve its sustainability goals.
How to Prepare for Energy Audit in Manufacturing?
The depth of the energy audit is up to the manufacturer. You can choose a light audit, which only looks at a handful of manufacturing systems at a high level. Or you can choose an in-depth analysis. It all depends on your energy-saving goals. Governmental entities often provide funding to help manufacturing organisations carry out an energy audit, as energy efficiency is a goal that benefits society in general.
What Happens During an Energy Audit?
An energy audit is a systematic and thorough process that evaluates your facility’s energy usage and identifies opportunities to enhance energy efficiency. There are three main phases of an energy audit;
Here’s a breakdown of what typically happens during an energy audit, presented step-by-step:
1, Initial Consultation and Scope Definition
2. On-Site Assessment
3. Operational Context Gathering
4. Analysis of Energy Usage
5. Recommendations and Prioritisation
6. Financial and Sustainability Insights
7. Strategic Decision-Making Tool
8. Follow-Up and Monitoring (Optional)
By uncovering hidden inefficiencies and providing a roadmap for improvement, an energy audit in manufacturing sets the stage for cost savings, improved operational performance, and a reduced environmental impact. It’s more than just a one-time process—it’s an investment in the future of your business.
What is Assessed in a Energy Audit for Manufacturing?
The on-site visit can take as little as a few hours, or a full day, depending on the agreed scope of audit. Here are some of the areas, machines and processes that are typically assessed in an energy audit:
For each area, machine and process assessed, an auditor is typically looking at these:
Physical State, Function and Energy Usage
Examples of physical state, function & energy usage assessed in an energy audit:
What is an Energy Audit Report?
An energy audit report is the comprehensive output of an energy audit, providing detailed insights into a facility’s energy usage, inefficiencies, and opportunities for improvement. It serves as a roadmap for enhancing energy efficiency, reducing energy costs, and lowering the facility’s carbon footprint.
Key components of an energy audit report include:
This report not only helps businesses make informed decisions about implementing energy-saving measures but also acts as a long-term reference for planning future upgrades and investments. It’s an essential tool for achieving energy savings, improving operational efficiency, and ensuring sustainable growth.
How to Fund an Energy Audit?
Funding an energy audit can be a straightforward process, thanks to various government grants, tax incentives, and energy-efficiency programmes available worldwide. These options not only make audits affordable but also encourage businesses to adopt energy-saving measures and reduce their carbon footprint.
Global Funding Options
Narrowing Down to Ireland
In Ireland, the government offers grants of up to €2,000 for conducting an energy audit. In most cases, this grant covers the entire cost, making it an excellent opportunity for manufacturers to evaluate and optimise their energy usage without a significant financial burden. To learn more about the Irish scheme or to apply, businesses can visit the SEAI website for detailed information and application steps.
By leveraging these funding opportunities, businesses can not only offset the upfront cost of an energy audit but also unlock long-term cost savings and operational improvements. Whether it’s through grants, tax breaks, or utility support, funding options exist globally to make energy audits accessible and impactful.
Bottomline
To find energy efficiencies on your own, or to make the most of an energy audit’s recommendations, you’ll need an Energy Management System. An Energy Management System is a solution for measuring and monitoring your operation’s energy usage. Contact Mavarick today to learn about our solutions for manufacturing production and energy management.
FAQs About Energy Audits in Manufacturing
What is an energy audit, and why is it important?
An energy audit is a detailed evaluation of a facility's energy usage to identify inefficiencies, reduce energy costs, and improve overall energy efficiency. It’s crucial for minimising your carbon footprint and achieving long-term energy savings.
How long does an energy audit take?
The duration varies depending on the size and complexity of the facility. Most energy audits in manufacturing take anywhere from a few days to several weeks, depending on the scope of assessment.
What are the key benefits of an energy audit in manufacturing?
An energy audit provides insights into energy consumption, highlights opportunities to save energy, reduces utility bills, and supports compliance with environmental regulations. It also helps in achieving sustainability goals by lowering emissions.
Who should conduct an energy audit?
Certified energy auditors or energy efficiency consultants are ideal for conducting energy audits. They have the expertise to evaluate systems like air conditioning, machinery, and processes effectively.
What happens after the energy audit?
You receive a comprehensive report detailing energy inefficiencies, recommended energy-saving measures, and a roadmap to reduce energy costs. It serves as a guide for implementing changes to optimise operations and drive sustainability.
Carbon Accounting System
Carbon Emissions Reporting for the Supply Chain
- Visible Supply Chain
- Quality Data You can Trust
- Auditable Reports