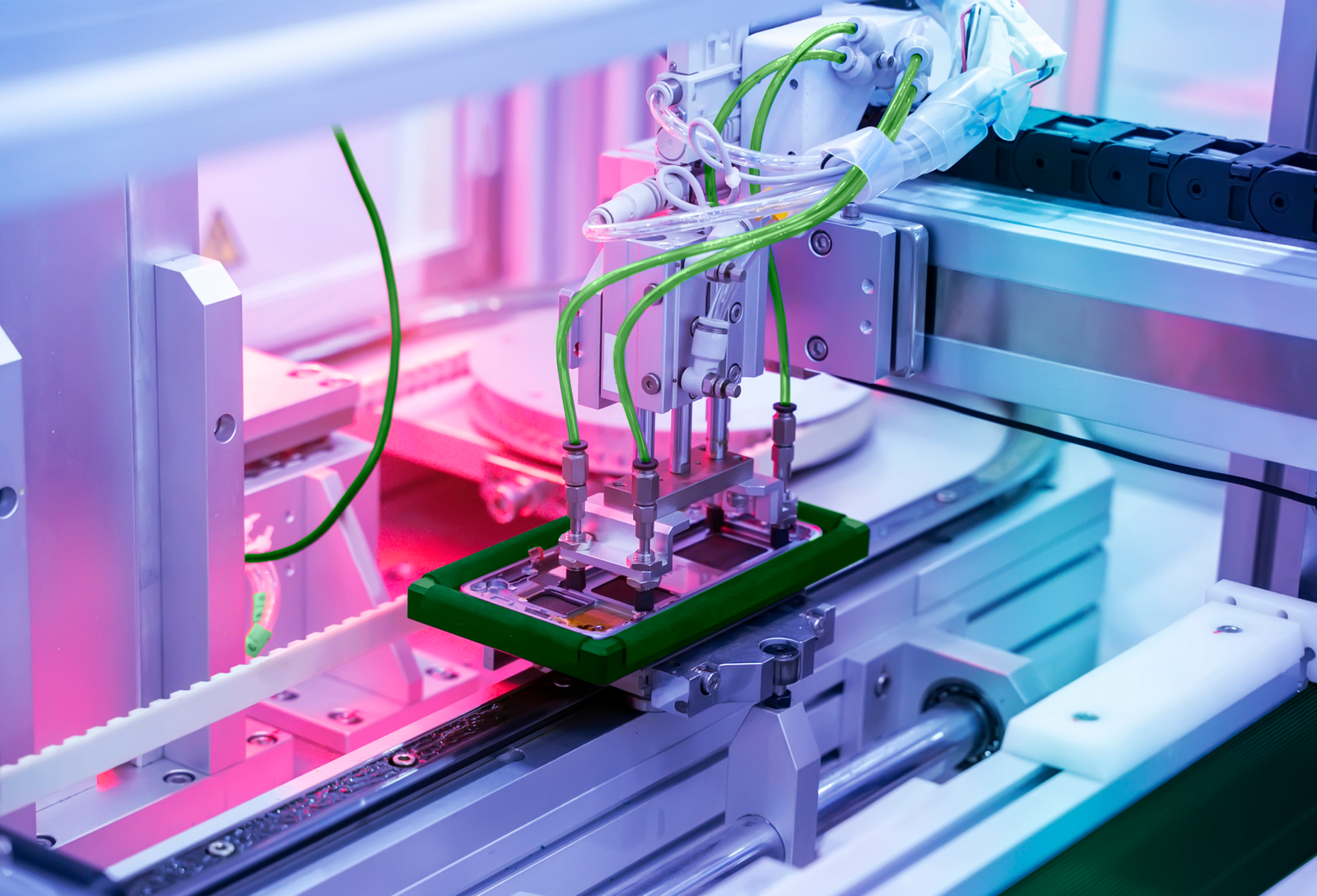
Table of Contents
- What is Downtime in Manufacturing?
- Types of Manufacturing Downtime
- What is Planned Downtime?
- Planned Downtime – Scheduled Maintenance
- Planned Downtime – Changeover
- Planned Downtime – Not Running Shifts
- What is Unplanned Downtime?
- Unplanned Downtime – Unscheduled Maintenance or Breakdown
- Unplanned Downtime – Configuration Error or Changeover Error
- Unplanned Downtime – Lack of Material
- Unplanned Downtime – No Operator Available
- How to Identify the Root Cause of Manufacturing Downtime
- Identifying Root Cause of Downtime - Manual Audits
- Identifying Root Cause of Downtime - Team Communication
- Identifying Root Cause of Downtime - Automated Methods
- How to calculate Cost of Downtime in Manufacturing
- How to Reduce Downtime in Manufacturing
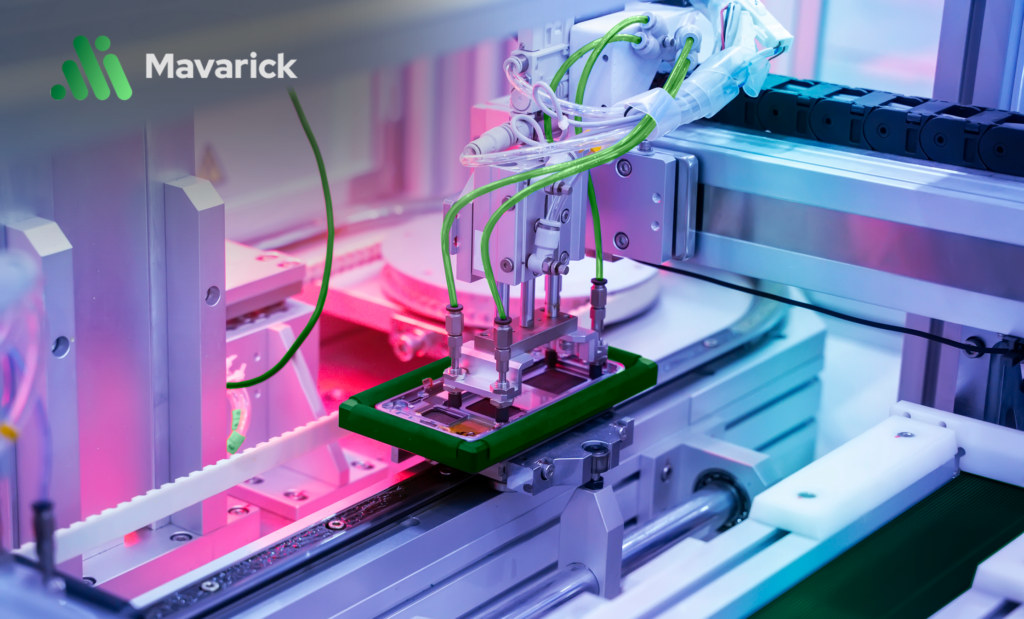
Downtime in manufacturing is an unavoidable reality. Value add operational downtime events such as servicing and tool set ups are inevitable components of the manufacturing process. These are inherent costs associated with manufacturing operations. Non-value add downtime events however, represent a distinct challenge. As a manufacturer, your primary objective should be to minimize unplanned downtime as it negatively impacts your bottom line and factory capacity.
In this article, you’ll learn:
- What is downtime in manufacturing?
- What are the different types of downtime?
- How to identify causes of downtime
- How to calculate costs of downtime
- How to reduce downtime in manufacturing
Downtime in manufacturing is an issue that is best addressed using machine monitoring software. For more on machine monitoring, see our Complete Guide to Machine Monitoring.
What is Downtime in Manufacturing?
A definition for downtime in manufacturing is very simple:
Downtime occurs whenever a manufacturing machine is not producing product. As discussed, some downtime events are inevitable. But if you want to maximise production in your manufacturing operation, and if you want to maximise profitability of your manufacturing business, you need to minimise unplanned downtime.
Types of Manufacturing Downtime
Downtime can be categorised as :
- Planned downtime
- Unplanned downtime
The first is inevitable. The second must be minimised.
What is Planned Downtime?
Planned manufacturing downtime is downtime that occurs by design. Manufacturing can be a very complicated business, and there are many reasons why an operation may need to plan to shut down machines . We’ll cover a few here.
Planned Downtime – Scheduled Maintenance
The most common type of planned downtime, and the easiest to identify, is scheduled maintenance. Manufacturing takes a heavy toll on the machines they depend on. "Preventive" maintenance is a well-known practice among manufacturers. In preventive maintenance, manufacturers perform maintenance before there is a breakdown. Preventive maintenance can occur according to a pre-planned schedule, or it can occur when machine monitoring software alerts an operator of an imminent issue. Either way, the machine must be shut down for preventive maintenance to take place. Both pre-planned, scheduled maintenance and just-in-time maintenance are considered “planned” downtime.
Planned Downtime – Changeover
Manufacturers don’t produce the same product forever. Inevitably, a manufacturer must change their machine set ups to produce a new type of product. For example – a maker of orthopedic devices may need to change the cutting tools required to produce different orthopedic knee sizes. Whenever you change from producing one product to another, you’re going to have downtime. These production swaps, called “changeovers”, are another inevitable type of planned manufacturing downtime.

Planned Downtime – Not Running Shifts
There may be times in your operation when it is not necessary to run every machine. A particular type of output product may not require a certain machine. Or you may be running a training session on that machine for new operators. It may seem glaringly obvious, but a premeditated decision not to run a particular machine needs to be included in “planned downtime”.
What is Unplanned Downtime?
Unplanned downtime occurs whenever a machine is scheduled to produce but is not in fact producing product. Very simple, very straightforward in theory. Trickier in practice.
Some example causes of unplanned downtime:
- Unscheduled maintenance / breakdown
- Incorrect configuration / changeover error
- Lack of materials
- No operator available
Unplanned Downtime – Unscheduled Maintenance or Breakdown
Breakdowns happen. Manufacturing can be a rigorous process. Machines take a lot of wear and tear and a lot is expected of manufacturing machines. Sometimes things break. Tools break. When this happens, manufacturing stops. Machine monitoring systems may help you detect issues before they turn into crises.
Unplanned Downtime – Configuration Error or Changeover Error
As mentioned before, all manufacturing operations need to transition from the production of one product to another. You can’t expect to manufacture the same thing forever. During a changeover process, it is necessary to reconfigure a machine to produce a different product or make a slightly altered version of the same product. When this happens, sometimes humans make errors as they update the machines for the new process. When this happens, it leads to unplanned downtime. Changeover or configuration errors differ from breakdowns or unscheduled maintenance, but they still lead to unplanned manufacturing downtime.

Unplanned Downtime – Lack of Material
Again, very self-explanatory. In the course of manufacturing product, you may find that you run out of one or another essential material input. It’s possible that your estimates for quantity levels were off. It’s possible that ordered inputs were not up to spec. It’s possible that raw materials were damaged or became damaged through the manufacturing process at a higher-than-expected rate. The result is the same; if you run out of raw materials, you must cease production.
Unplanned Downtime – No Operator Available
You schedule shifts as precisely as you can, but you can’t always predict human behaviour, or know what other priorities may occur for your workforce or human health. Your operator may be pulled away from their schedule for several reasons, such as attending to priority order requirements. They may also be pulled away due to unforeseen personal circumstances. When your workforce requires isn’t available sometimes machines will need to be left idle. These are examples of unplanned downtime.

How to Identify the Root Cause of Manufacturing Downtime
Every manufacturing operation seeks to minimise unplanned downtime. They say that time is money, and there may be no place where that is more applicable than in manufacturing. If you want to minimise downtime, then you’ll have to develop skills and methods for identifying root causes of downtime.
Identifying Root Cause of Downtime - Manual Audits
A manual audit is the most basic form of root-cause-analysis for manufacturing downtime. Performing a manual audit simply requires a person to walk the shop floor, usually with a notebook & pen, to inspect the machines one by one. The performer of a manual audit notes which machines are on and which are off and tries to determine why a machine might be off. In the process of investigating this question, the manual auditor may consult the machine controller. Machine controllers sometimes provide indications as to the reasons a machine may have been switched off. Alternatively, the performer of a manual audit may need the input of operators. The auditor may interview an operator to get context around a machine’s issues. This can be done in a ad hoc manner, or through a scheduled review of processes.
Identifying Root Cause of Downtime - Team Communication
Some manufacturing teams schedule regular check-ins with team members, to review progress against orders and to dig into issues. These feedback sessions can provide forums for investigating drivers of downtime. Unfortunately, human error and human bias can lead to complications when trying to identify root causes of manufacturing downtime when using “team communication” or individual operator interview methods. People are prone to biases when it comes to their own recollections of events. For example – operators may consider downtime drivers that occurred more recently to be more important than those that occurred further in the past. This is called “recency bias” and is very common. Another human bias to consider is the tendency to give greater importance to large, lengthy downtime incidents (which happen infrequently) - as opposed to smaller more common incidents. It may be the case that common, smaller downtime incidents occur frequently enough to represent the largest overall driver of downtime.
However – the common nature of these types of downtime incidents can render them less memorable than larger, rarer downtime incidents. For example, human operators may not consider the downtime that results from transporting material from outside a warehouse to the factory floor where it is fed into manufacturing operations. Operators may consider the transportation time to be a simple cost of business, and thereby neglect to include it in their estimations of downtime. Because of this, relying on human feedback and memory to investigate downtime causes can be problematic.
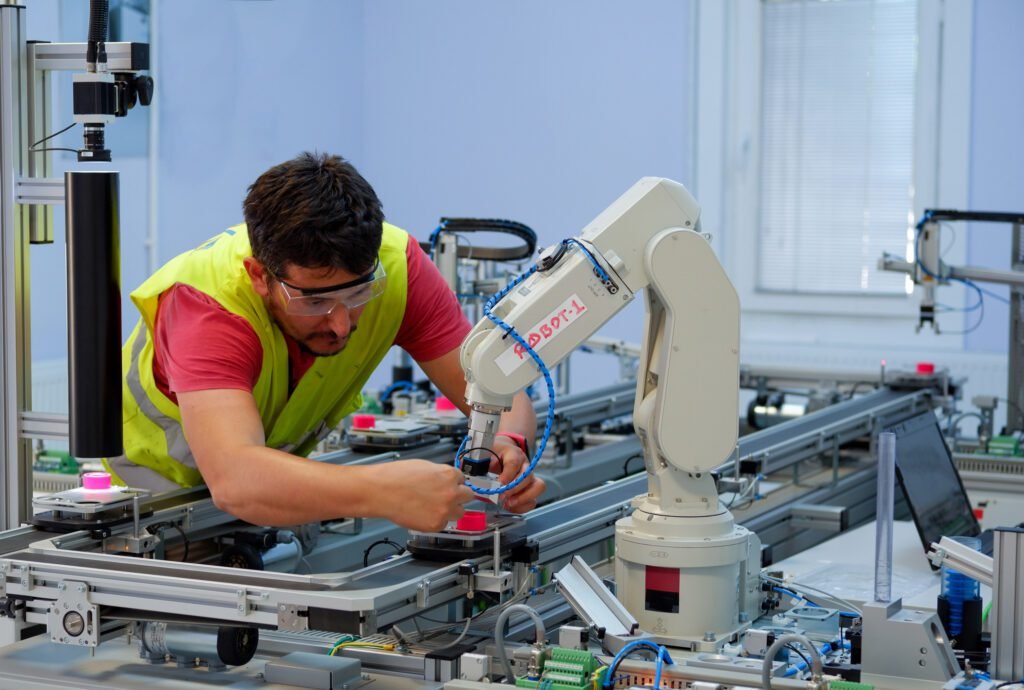
Identifying Root Cause of Downtime - Automated Methods
By far, the most reliable methods for identifying root causes of downtime are automated methods. Machine monitoring systems can be configured to track the health and activity of every machine on your shop floor – and are not prone to biases. Automated monitoring systems are especially useful when tracking more common types of downtime and aggregating them to understand the overall impact of different downtime causes. Typically, machine monitoring systems are configured to present pre-set "reason codes” for different downtime causes, such as “Tool Breakage” or “No Material”. Operators select the appropriate cause for each incident so that downtime can be analysed in aggregate within the centralised software interface. Automated machine monitoring systems can help manufacturing operations understand the largest drivers of downtime and identify time periods that are more prone to downtime than others.
How to calculate Cost of Downtime in Manufacturing
The cost of downtime in manufacturing can be calculated through a straight-line analysis of the value of the machine. Manufacturers typically bill by the hour, by the machine, when producing product for end clients. Because of this, manufacturers have a very straightforward method for understanding the value of any hours that a machine is left idle. Let's take a simple and conservative example; if a machine is scheduled to be active for 15 hours a day, at €100 billed per hour – and that machine is down for 5 of those 15 hours, then your downtime has cost you €500 in potential billing - for just one machine in one day. It soon adds up. For industrial manufacturers the costs of unplanned downtime can be huge and are estimated to be $50bn each year. The cost of downtime can be calculated by looking at the capacity a machine could have been scheduled for but was out of action due to downtime.
How to Reduce Downtime in Manufacturing
When any organisation purchases a new software solution, they typically have a desired business outcome for that software. For machine monitoring software, the business outcome that manufacturers are seeking is to reduce downtime. The secret to minimising downtime is in the rapid and accurate identification of the cause, the aggregation of different causes, and the correct prioritisation of remediation efforts:
- Identify that unplanned downtime is occurring
- Identify the cause of the downtime
- Aggregate data on cause of downtime, time of occurrence, and duration of downtime
- Prioritise remediation based on the total cost of the downtime & the ease of remedy
Automated aggregation of downtime causes, time of occurrence and duration allows manufacturers to understand the largest drivers of downtime over different periods of time. Once the largest drivers of downtime are identified, remediation is prioritised via three factors: the business impact of the downtime, the cost of remediation, and the ease with which a remedy can be carried out. Obviously, foregone revenues are a strong driver when determining how to prioritise efforts to remedy downtime causes. Downtime causes that result in higher overall losses will naturally be top of mind for manufacturers. But a manufacturer must also consider the cost to correct for downtime causes, and the ease with which causes can be remedied. Downtime solutions that are easy and cheap to deploy may sometimes be prioritised above those that are causing a greater impact to the business. However you choose to prioritise downtime remediation, machine monitoring software will help you to make more accurate and impactful decisions. Contact Mavarick Todayto learn how you can reduce downtime in your manufacturing operation.
Carbon Accounting System
Carbon Emissions Reporting for the Supply Chain
- Visible Supply Chain
- Quality Data You can Trust
- Auditable Reports